

programcx
- 粉丝: 44
- 资源: 13万+
最新资源
- 自动折盒贴标机sw16可编辑全套技术资料100%好用.zip
- 平安夜祝福+圣诞树代码,巨漂亮,心动
- 基于Springboot+Vue健身房管理系统源码+数据库+视频教程+文档
- 用户登录数据库SQL,用户登录数据库
- 300元花钱买来的一款企业发卡程序源码+短链接+二维码修复(站长亲测)
- Java毕业设计-基于Springboot+Vue健身房管理系统源码+数据库+视频教程+文档
- 基于springboot+vue的健身管理平台源码+数据库+视频教程+文档
- Java毕业设计-基于springboot+vue的健身管理平台源码+数据库+视频教程+文档
- C#常用工具类源代码(Excel操作类 FTP操作类 JSON操作类等等)
- 多线程扫描文件夹下的文件
- HENU河南大学 计算机学院 计网期末复习知识点
- CNC封闭式自动化上下料设备step全套技术资料100%好用.zip
- 伺服电机驱动机械臂step全套技术资料100%好用.zip
- 用户登录界面,验证成功界面,数据库
- 侧吸式油烟机sw16可编辑全套技术资料100%好用.zip
- 新界面企业版自动售卡发卡平台系统网站源码对接易支付接口
资源上传下载、课程学习等过程中有任何疑问或建议,欢迎提出宝贵意见哦~我们会及时处理!
点击此处反馈


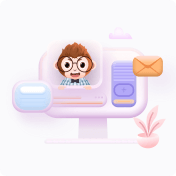
评论0