1. ModScan Overview
1.1 Document/View Architecture
1.2 Modbus Data Definition
1.3 Display Formats
1.4 Connecting to a Modbus Network
1.4.1 Direct Serial Connections
1.4.2 Modem Connections
1.4.3 Network Connections
2. Menu Commands
2.1 File menu
2.2 Connection menu
2.3 Setup menu
2.4 View menu
2.5 Window menu
2.6 Help menu
3. Tool & Status Bars
3.1 Toolbar
3.2 Format Selections
3.3 Status Bar
4. Testing Features
4.1 Writing Data to the Modbus
4.2 Message Counters
4.3 Observing Serial Traffic
4.4 Capturing Data to Text File
4.5 User Defined Commands
4.6 Scripts
5. Using ModScan with a Database
6. Using OLE Automation
6.1 Overview
6.2 Automation Routines
7. Distribution/Registration
7.1 Pricing
7.2 Licensing
7.3 Support
7.4 Other Products
1. ModScan Overview
The ModScan application operates as a MODBUS mastermodbus_protocol device
in either RTU or ASCII transmission modes. ModScan may be used to access
and modify data points contained in one or more MODBUS slave devices
connected to the PC via a serial port, modem, or network. ModScan supports
the standard MODBUS message types 01-06, 15 & 16, as well as providing
the ability for you to exercise special features of a slave device by
transmitting custom command strings and observing the response. ModScan
is a useful test and diagnostic tool for verifying the proper slave
response to MODBUS queries as well as being a low cost data collection
tool for interfacing data into PC database and spreadsheet applications.
1.1 Document/View Architecture
ModScan utilizes the standard Windows Multiple-Document-Interface, (MDI),
architecture for displaying modbus data to the user. Each document
represents a series, (array), of modbus data points identified by the
following parameters:
Slave Device Address Represents the physical device attached to
the modbus network
Data Type Internal data representation, (i.e. input, coil, register)
Data Address Point address within the device
Length Number of points to scan/display
Associated with each document is also a timer, which is used to
periodically scan new data from the defined slave and refresh the
display. The modbus data definition is accessible from the ModScan
menu or via edit controls in the top splitter window of the document
display. As new data is obtained from the slave device, it is
written to the bottom splitter window in one of several formats,
depending upon your preference. The size of each document display
window is adjustable via the splitter control.
1.2 Modbus Data Definition
The upper half of each Document's View represents the data selected for
display, (and possible capture to a historical data file). In most
testing applications, the ModScan will only be connected to a single
modbus slave device, however, in a multidrop modbus network, there may
be several devices accessible from a single connection. The "Device Id"
edit control allows you to specify the slave address for the source of
the data. Likewise, edit controls are available to select the point
type, data address, and number of data points to access.
Notice that the modbus protocol uses a 5-digit representation for the
slave data address which infers the point-type. For example,
INPUT STATUS values are always represented in the range 10001-19999:
HOLDING REGISTERS are displayed as 40000-49999. The ModScan application
uses the standard notation for displaying data in the bottom splitter
window, however the address specified in the upper splitter address edit
control assumes a 4-digit physical point address. This address, coupled
with the point-type specifier completely defines the data to be accessed
in the slave device.
The upper splitter window also contains two counters which are used to
tally the number of data requests made from this document to the modbus
connection and the number of valid slave responses received in reply.
A button is available within the display which resets the counters
associated with this document.
1.3 Display Formats
As data is received from the slave device, it is displayed to the lower
splitter view of the associated document. Any errors incurred during
the exchange of information will be displayed on the first line. The
font and colors used to display the data is configurable via the View,
Config menu options.
Modbus register data may be displayed in any of the following formats:
Binary Data displayed as 16 discrete values.
Decimal Ranges from -32767 to 32768
Hexadecimal 0000-ffff
Floating Point IEEE Standard Floating Point Notation
(Requires two registers per value)
Word-Swapped Floating Point
Inverted Floating Point used by some processors
Double-Precision Floating Point
64-bit Floating Point Notation
Word Swapped Dbl Precision
Inverted 64-bit Float Values
1.4 Connecting to a Modbus Network
1.4.1 Direct Serial Connections
ModScan may be used to obtain data from modbus slave device connected
to the PC in one of three basic physical arrangements. The most common
connection is via any one of the four available PC serial COM ports.
ModScan uses the standard Win32 software drivers for communication with
the COM ports, thereby providing support for any hardware serial boards
which may be installed in the Windows operating system, (including RS-232,
RS-485, etc.). You have complete control over the operating characteristics
of the serial connection by selecting the appropriate baud rate, parity,
and control line, (handshaking), properties to match the slave device(s).
1.4.2 Modem Connections
In remote testing situations, the ModScan application may be used to
communicate with a modbus network over a dedicated modem connection.
ModScan supports the TAPI, (telephony application interface), standard
implemented in Windows and Windows NT. If selected, the modem connection
dialog allows you to enter a phone number for dialing. Any TAPI device
configured within the Windows operating system is available for use.
It is also possible to connect via modem to a remote system utilizing
the built-in networking characteristics of Windows '95 & NT. To do this,
you will need to configure the ModScan application to connect via a TCP/IP
connection which has been setup within Windows to automatically dial and
establish a PPP connection with another Windows machine which is connected
directly to the slave device(s) you wish to use. In this case, ModScan
operates as if it were using a network card connected directly to a
modbus to tcp/ip bridge device.
1.4.3 Network Connections
ModScan allows modbus communications to occur over a TCP/IP network.
This feature requires the use of a modbus to TCP/IP bridge device which
can service network requests from the network and obtain the data from
a connected slave device prior to responding to queries from the ModScan
application. A bridge device operates as a network server, providing
support to numerous client applications distributed over the network.
WinTECH Software provides such a server for interfacing to a single
serial modbus network. Third-party vendors may provide various solutions
for interfacing TCP/IP to modbus devices via other hardware, (i.e. modbus
plus, etc.). If the interfacing specification for these network bridge
devices is available in the public domain, they may be included in future
releases of the ModScan application. If you have the need to use ModScan
with a third-party vendor's equipment, please contact the WinTECH Software
support line for consideration.
2. Menu Commands
2.1 File menu
The File Menu offers the following commands:
New Creates a new ModScan document. Each document represents
a different block of data from a modbus device.
Open Opens an existing document.
Close Closes an open document.
Save

OKGOGO1
- 粉丝: 8
- 资源: 8
最新资源
- 该仿真主要应用于路径规划和轨迹跟踪的研究 主要有五个文件(内部包含3个算法,两个仿真),1.A星算法自动生成避障的最短路径,2.两轮小车及其四轮小车的运动学建模3.纯路径跟踪算法,包括预锚点的选择算
- Edifier Connect_8.4.11.apk
- anaconda配置pytorch环境.md
- 机械设计自动倒角机sw18可编辑非常好的设计图纸100%好用.zip
- 基于28027滑膜算法的水泵驱动方案,带有初始定位算法,启动不反转,pfc采用硬件方案
- 机械设计自动PCM板胶纸机sw18非常好的设计图纸100%好用.zip
- 三相PWM整流器闭环仿真,电压电流双闭环控制,输出直流电压做外环 模型中包含主电路,坐标变,电压电流双环PI控制器,SVPWM控制,PWM发生器 matlab simulink模型 功率因数1,低TH
- anaconda配置pytorch环境.md
- Cytoscape-3-10-3-windows-64bit-仅限个人学习
- DDR3测试模块 fpga测试接口模块,提供测试模块工程 Vivado2019.1或者Vivado2017.4;语言vhdl 可以修改ip引脚,测试初始化完成
- 网络工程领域竞赛试题:网络搭建与应用的技术实战项目
- 山东大学软件学院人工智能导论22级复习资料
- 机械设计自动切断面条机ZD80sw16非常好的设计图纸100%好用.zip
- 毕设基于stm32的风机监控系统程序设计源码.zip
- 机械设计自动贴E型定位胶纸机sw18非常好的设计图纸100%好用.zip
- 机械设计自动贴E型胶纸机sw18非常好的设计图纸100%好用.zip
资源上传下载、课程学习等过程中有任何疑问或建议,欢迎提出宝贵意见哦~我们会及时处理!
点击此处反馈


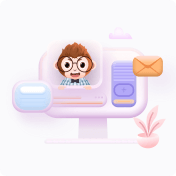