
文档爱好者
- 粉丝: 8
- 资源: 29万+
最新资源
- Navicat.zip
- 麻雀搜索算法(SSA)文章复现:《基于混沌麻雀搜索算法的无人机航迹规划方法-汤安迪》 策略为:立方混沌+反向学习初始化种群+反向精英策略改进发现者策略+正余弦算法改进加入者策略+动态调整警觉者
- “田园风光在线”:打造村旅游信息平台
- Ollama.zip大模型
- 土地利用/土地覆盖数据(蚌埠市)对应代码表
- 基于Unity 3D的旅游景点漫游设计
- 基于混沌-高斯变异-麻雀搜索算法(CGSSA)优化BP神经网络(CGSSA-BP)的回归预测(含优化前后对比)MATLAB代码 代码注释清楚 main为主程序,可以读取EXCEL数据 很方便
- xyy_localhost-2024_12_24_14_32_06-dump.sql
- C++模板与泛型编程入门教程:代码重用与类型安全
- 面向对象编程语言Objective-C基础语法详解及应用
- MATLAB在ThingSpeak中应用信号处理与数据可视化的技术实现
- VMware.zip虚拟机
- CFA知识点梳理系列:CFA Level II, Reading 6 Economic Growth
- goland 2024直接使用到2099年
- SecureCRT-9.6.0-mac
- Python 自动办公- Python分类汇总278张Excel表中的数据 Python源码
资源上传下载、课程学习等过程中有任何疑问或建议,欢迎提出宝贵意见哦~我们会及时处理!
点击此处反馈


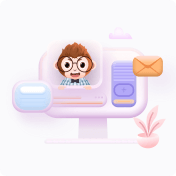