
lpmkonji_
- 粉丝: 1
- 资源: 5
最新资源
- 风光储VSG并网,储能为锂电池 0.6s引入预同步算法,实现稳定并网 工况多,波形好
- 同步磁阻电机SynRM无传感器高频注入HFI+mras驱动matlab离散模型,包含文献,用于学习研究
- 基于粒子群算法的光伏MPPT(可重启PSO) 光伏最大功率追踪算法模型simulink MPPT是基于粒子群算法实现的,同时具备动态追踪能力,当光照改变后会重启粒子群算法进行最大功率追踪
- Comsol等离子体仿真,Ar棒板流注放电 电子密度,电子温度,三维视图,电场强度等
- 储能参与调峰调频联合调度模型(matlab代码) 主要内容为考虑储能同时参与调峰以及调频的联合调度模型,现有文章往往仅关注储能在调峰方面的能力,而实际上同时参与调峰调频将超线性的提高储能的收益,在建模
- Matlab simulink仿真模型搭建(电池相关) 本店可接锂电池或电池包建模搭建 单体电池方面: 1、电池等效电路模型搭建(RC模型) 2、电池特征参数辨识(离线、在线、自适应) 3、电池SOC
- 三相并网逆变器双闭环控制,电网电流外环电容电流内环控制算法,matlab Simulink仿真模型,有源阻尼,单位功率因数,电网电压和电流同相位
- 脉振高频电压注入的永磁同步电机无速度传感器 PMSM
- 三相电压型PWM pwm整流器仿真,双闭环pi PI控制(电压外环电流内环),输出电压600V,单位1运行,变负载实验
- 基于下垂控制的三相全桥PWM逆变器并网仿真模型 基于Matlab Simulink仿真平台 主电路采用三相全桥PWM逆变器 1.仿真均能正常运行,能够准确跟踪对应参考值 2.直流母线电压设置为700V
- 基于扩展反电动势法的PMSM中高速无感控制仿真,对凸极和非凸极电机都适用,模型全部采用离散化的仿真方式,仿照数字控制器真实的特性,有PI+PLL和PI+Luenberger两个版本,龙伯格观测器角度估
- 两极式单相光伏并网仿真 前极:Boost电路+电导增量法 后极:桥式逆变+L型滤波+电压外环电流内环控制 并网电流和电网电压同频同相,单位功率因数并网,谐波失真率0.39%,并网效率高
- 国标GBT34658-2017直流快充27930一致性测试详细报告 对测试用例进行了详细测试,含有通过的BMS快充报文内容 注:同时增加了对测试用例分析和软件兼容性做法
- Comsol等离子体仿真,空气棒板电晕放电 电场强度等
- STM32三相电压型SVPWM整流器仿真,以电压外环和电流内环控制,双闭环PID控制,输出电压600V 三相电压型SVPWM整流器仿真,以电压外环和电流内环控制,双闭环PID控制,输出电压600V
- 电机maxwell Simplorer耦合模型,Maxwell 中建立BLDC电机本体有限元模型,Simplorer中搭建的SVPWM策略下Id=0双闭环控制外电路模型 可成功实现场路耦合联合仿真
资源上传下载、课程学习等过程中有任何疑问或建议,欢迎提出宝贵意见哦~我们会及时处理!
点击此处反馈


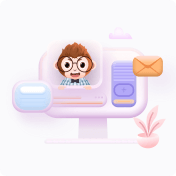