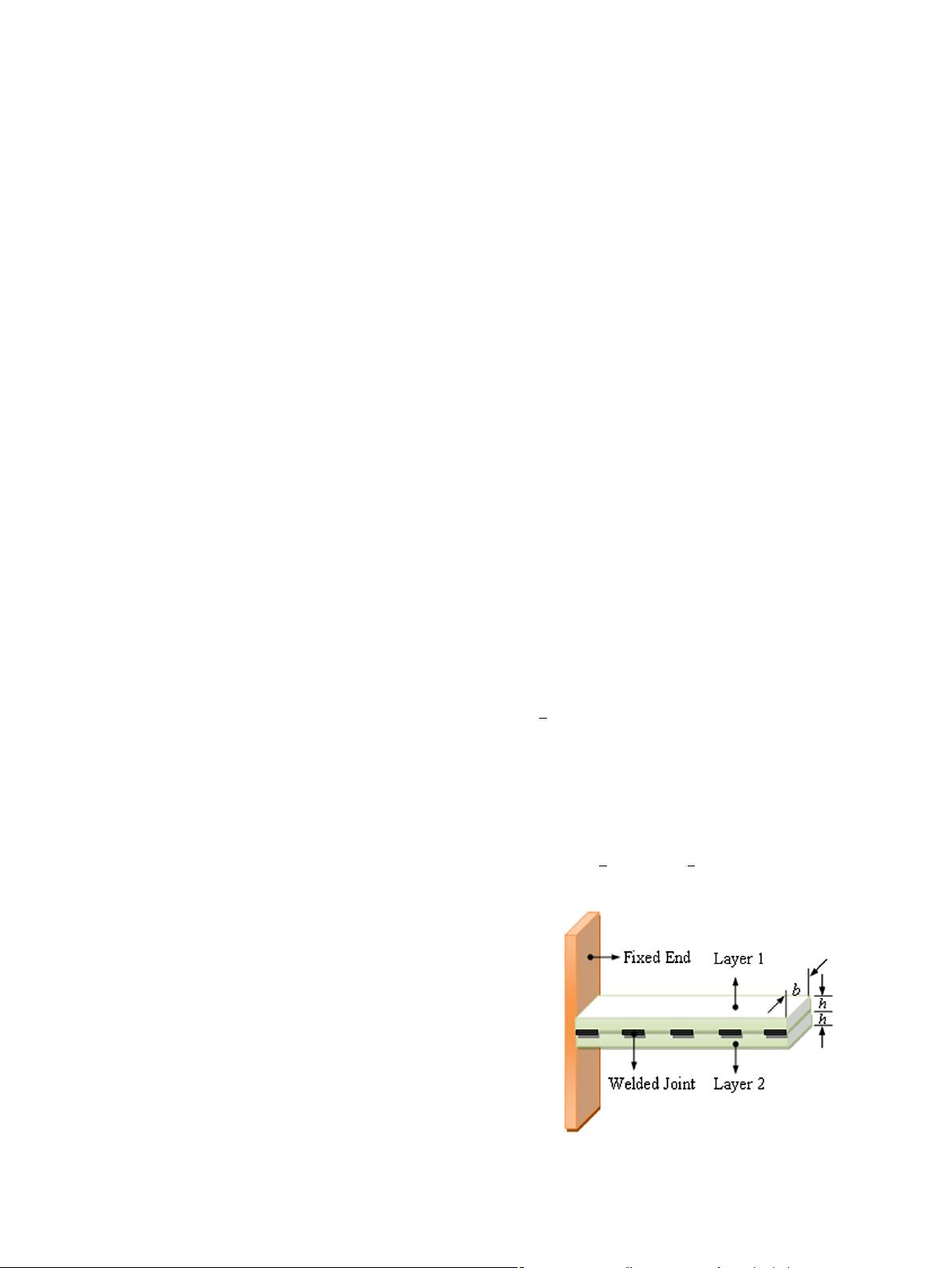
Further, Masuko et al. [9], Nanda and Behera [12] examined the
interfacial slip damping in layered bolted structures and developed
a theoretical expression for the pressure distribution at the inter-
faces of a bolted joint by curve fitting the earlier data reported
by Ziada and Abd [13]. They further extended their work by devel-
oping a generalized mathematical expression for the logarithmic
damping decrement of such structures with multiple interfaces.
Nanda and Behera [14,15] and Nanda [16] further studied the dis-
tribution pattern of the interface pressure as well as the damping
capacity of layered and jointed structures by carrying out numeri-
cal analysis and performed experiments to ascertain the effects of
number of layers, diameter of bolts and use of washers on the
damping characteristics. However, their study is limited to the sta-
tic loading without considering the effect of in-plane bending
stresses on the dynamic slip and damping capacity.
The effect of non-uniform interface pressure distribution on the
mechanism of slip damping for layered beams has also been exam-
ined recently by Damisa et al. [17] limiting their analysis to static
loads and linear profiles of interface pressure distribution. How-
ever, Olunloyo et al. [18] have considered other forms of interfacial
pressure distributions such as; polynomial and hyperbolic and ob-
served large difference in the results compared to the work of
Damisa et al. [17]. Although all these researchers considered the
in-plane distribution of bending stresses but their analysis is lim-
ited to the structures subjected to static loads.
More recent works in this area include Vitelleschi and Schmidt
[19] considering the effects of surface finish, Beards and Williams
[20] on rotational slip, Jezequel [21] on a plate-theory analysis,
Groper [22] on micro- and macro-slip in bolted joints, Wettergren
[23] and Csaba [24] on the role of microslip in generating damping
and reducing the dynamic instability of turbine generators.
In the recent years, researchers have focused their attention on
the role of interlayer slip in damping and dynamic behavior of lay-
ered and jointed engineering structures. Recently, Batista et al. [25]
studied the behavior of multilayered composite beams with inter-
layer slip, under Euler–Bernoulli as well as Timoshenko beam the-
ory assumptions. They presented analytical formulations for the
linear case, based solely on the interlayer slips, which allows easy
determination of closed-form solutions for statically determinate
beams. Further, they addressed slip or curvature locking problems
for the multilayered case. Challamel and Girhammar [26] investi-
gated the lateral-torsional stability of vertically layered composite
beams with interlayer slip, based on a variational approach. Loo
et al. [27] discussed the results of numerical analyses of timber
shear walls with slip-friction connectors instead of traditional
hold-down connectors. The results suggested that the slip-friction
connectors are efficient dissipaters of seismic energy during the
event of seismic overloading.
Finite element methodology has also been used effectively to
evaluate the damping mechanism of jointed and layered civil
structures. Law et al. [28] developed a hybrid finite element model
of a slotted bolted connection element (SBCE). The damping mech-
anism of this structure is based on the micro-slip elements in the
contact surface, and the damping properties can be designed for
any specific requirements by adjusting several design parameters
which in turn, depends on the physical parameters of the joint.
Further, they reported simulation studies on the vibration mitiga-
tion of a suspension footbridge due to pedestrian loading with 28
SBCEs. Recently, Larbi et al. [29] proposed 3D finite element model
in order to investigate the static and instantaneous behavior of
bonded connections between steel and concrete in the context of
composite beam bridges with high strength concrete. Boudaoud
et al. [30] adopted finite element methodology for the damping
analysis of sandwich beams with piezoelectric and viscoelastic
layers. They developed an analytical expression of the modal loss
factor and frequency of the sandwich beam, considering two feed-
back control laws.
2. Theoretical analysis
2.1. Static analysis
The two layered and tack welded cantilever beam model with
overall thickness 2h, width b, and length l as shown in Fig. 1ais
considered to find out the damping capacity. The loading consists
of uniformly distributed pressure at the interfaces due to the con-
tact between two flat bodies, and a concentrated static load P is ap-
plied at the free end, x = l. Each of the two halves of thickness h is
considered separately with the loading as depicted in Fig. 1b. The
continuity of stress and vertical displacement ‘v’ is imposed at
the interfaces. At some finite value of P, the shear stress at the
interfaces will reach the critical value for slip
s
xy
=
l
p where
l
and p are the kinematic co-efficient friction and interface pressure
respectively. Additional force due to excitation will produce a rel-
ative displacement
D
u(x) at the interfaces.
2.1.1. Interface pressure distribution
In the present analysis, the welded beams are considered to be
in contact with each other because of perfect flatness and same
condition of flatness is maintained under excitation due to weld-
ing. Since perfect contact is maintained under both the static and
dynamic conditions, the pressure at the interfaces is assumed to
be uniform. The contact pressure for flat surfaces with rounded
corners has been found out by Ciavarella et al. [31], which shows
a non-uniform distribution pattern at the interfaces. Contrary to
this, the pressure distribution at the interfaces is assumed to be
uniform owing to the contact of the upper layer over the lower
one. Therefore, the relation for uniform pressure distribution as gi-
ven by Johnson [32] and Giannakopoulos et al. [33] due to contact
of two flat bodies has been considered and the same is given by;
pðxÞ¼
P
b
ð1Þ
where P and b are the normal load per unit length and width of the
beam respectively.
2.1.2. Analysis of static response
The resultant moment at the centroid of each laminate as
shown in Fig. 1b is given by;
M
1
¼ M
2
¼ M ¼
P
2
ðl xÞ
l
pb
h
2
ðl xÞð2Þ
Fig. 1. (a) Two layered tack welded cantilever beam model and (b) two halves of
the beam depicting load and co-ordinates.
B. Singh, B.K. Nanda / Engineering Structures 48 (2013) 10–20
11