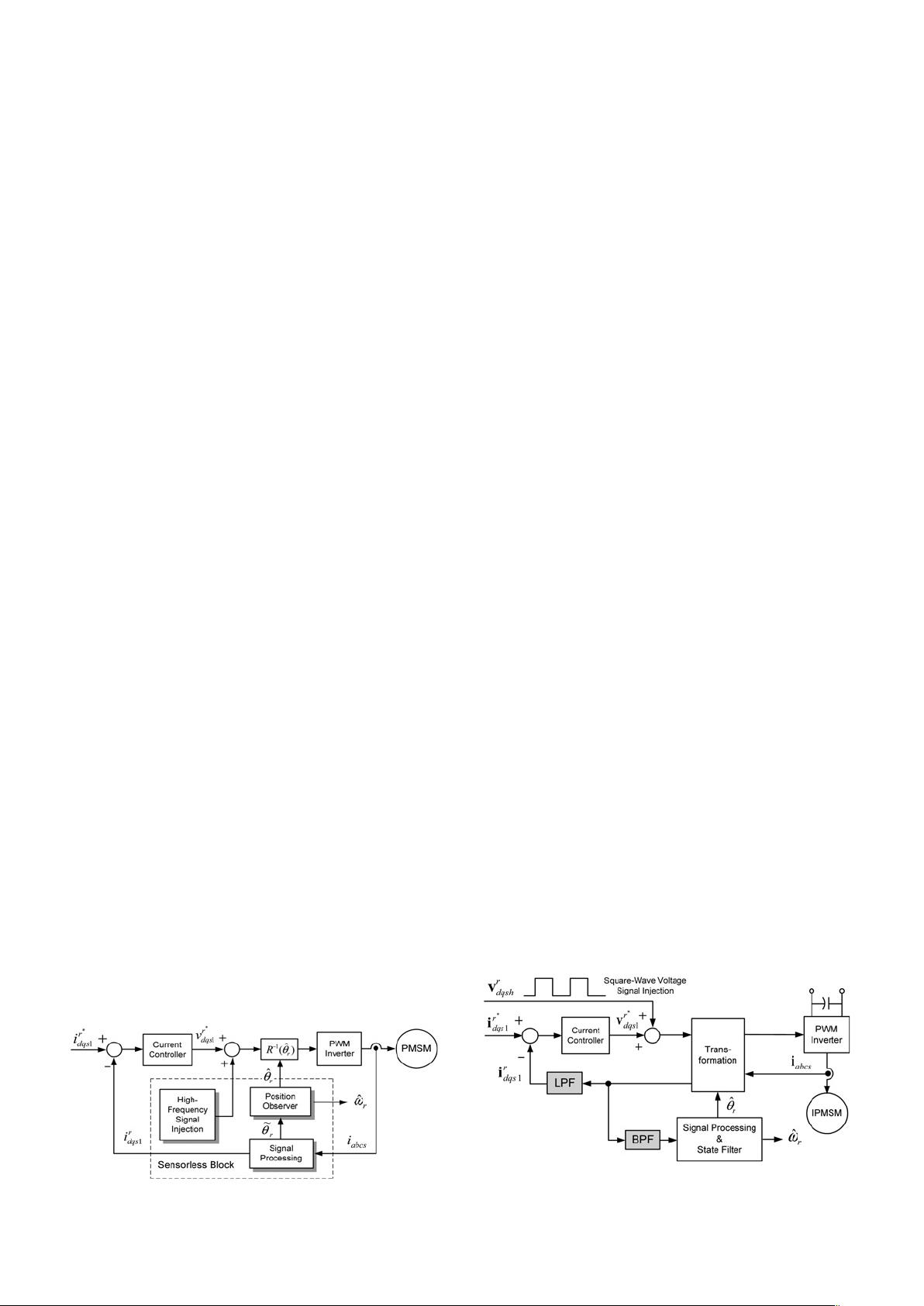
from the measured motor current. The time delay caused by
these filters as well as the time delay occurred in the
demodulation process are still obstacles to enhancing
bandwidths of current control and sensorless control.
This paper proposes an improved algorithm to provide an
easy implementation and an enhanced bandwidth of the
sensorless control based on the square-wave-type voltage
injection. First, in the proposed technique, the low-pass
filter to extract th e fundamental current is eliminated by
replacing it with a simple arithmetic operation. Second, the
band-pass filter to extract the injected frequency component
current is also replaced by a simple arithmetic operation.
Third, the time delay that occurred in the demodulation
process is reduced. Through eliminating the time delays
effectively in the signal process for the sensorless control
based on the square-wave-type voltage injection, the overall
algorithm can be much simplified so that its implementation
becomes easy and its dynamics can be improved. It was
verified that the proposed technique can enhance the
bandwidth of the speed controller in the sensorless drive by
the experiments on the 800 W IPMSM drive system.
Moreover, in this method, the initial rotor position can be
detected consistently by using the square-wave-type voltage
as a rotor-position detection signal for starting up th e
IPMSM. The proposed detection method can identify the
polarity of a permanent magnet by detecting the variations
in an inductance due to the saturation phenomenon of a
stator core.
2 Sensorless control based on
square-wave-type injection voltage
Fig. 1 shows a block diagram of a typical sensorless drive
based on the high-frequency signal injection. The sensorless
drive system consists of three parts. One is a
high-frequency signal injection part, which injects a special
signal continuously to obtain the saliency information of
the motor. Another is a signal processing part, which
decomposes the current induced by the injected voltage and
extracts the rotor position-related value. Lastly, there is a
position observer part, which estimates the rotor position
and the speed from the extracted rotor position-related value.
The performance and the complexity of the signal
processing and the position observer parts depend heavily
on the high-frequency signal injection part. In most
techniques, a sinusoidal voltage is commonly adopted as an
injection signal to obtain the saliency information. To
reduce the complexity of the sensorless control under this
injection signal, most works have been focused on the type
of signals that are measured and processed to obtain the
rotor position and the related signal-processing techniques.
However, recently, instead of the conventional
sinusoidal-type signal, a square-wave-type voltage injection
has been proposed to eliminate the low-pass filters required
for the signal processing and to enhance the control
bandwidth of the sensorless drives [10, 11]. In this case, the
square-wave-type injection voltage is described as
v
ˆ
r
dsh
(
v
h
t) =
V
h
half period
−V
h
otherwise
, v
ˆ
r
qsh
(
v
h
t) = 0 (1)
where the superscript
ˆ
r denotes the estimated rotor reference
frame, V
h
is the amplitude of the injection voltage and
ω
h
is the injection frequency. The maximum frequency of
the injection voltage, which has a significant influence on
the performance of the sensorless drive, depends on the
signal-processing technique to estimate the rotor position.
In the sensorless control based on the high-frequency
signal injection, even though the signal can be injected into
any reference frames, it is known that the voltage signal
injection into the d-axis of the estimated rotor reference
frame can result in a simpler signal processing and a better
performance [13, 14]. Thus, this paper will consider the
square-wave-type injection voltage of (1), which will be
added to only the d-axis output of the estimated rotor frame
current controller.
A block diagram of the sensorless control system using the
square-wave-type voltage injection is shown in Fig. 2.
Although this system can eliminate some low-pass filters in
the signal processing, it still requires a low-pass filter to
extract the fundamental current, which is used as a feedback
value to the synchronous frame current controller, from the
motor current. The time delay caused by this filter will limit
the bandwidth of a current control. A band-pass filter is
also required for extracting the injected frequency
component current with the rotor position information. The
delay caused by this filter will limit the frequency of the
injection signal and the dynamics of the sensorless control.
There are two popular signal-processing methods to obtain
the rotor position with the extracted high-frequency
component current. One method uses d- and q-axes induced
high-frequency currents in the stationary reference frame
[15, 16]. The other one uses the q-axis induced
high-frequency current in the estimated rotor reference
frame [17, 18]. In this paper, simple techniques to extract
the fundamental and the injected frequency component
currents withou t filters and an improved signal processing
to estimate the rotor position for both of these signal
processing methods are proposed.
Fig. 2 Block diagram of the sensorless control system by
square-wave-type voltage injection
Fig. 1 Block diagram of a typical sensorless drive
www.ietdl.org
IET Electr. Power Appl., 2014, Vol. 8, Iss. 2, pp. 68–75
doi: 10.1049/iet-epa.2013.0221
69
&
The Institution of Engineering and Technology 2014
评论0
最新资源