
mYlEaVeiSmVp
- 粉丝: 2270
- 资源: 19万+
最新资源
- Python 实现TCN-GRU时间卷积门控循环单元多输入单输出回归预测(含模型描述及示例代码)
- 创新流固耦合模拟煤层塌陷模型:基于fipy与pfc2d联合方法的多功能代码干货分享,创新流固耦合模拟煤层塌陷模型:基于fipy与pfc2d联合方法的多功能代码干货分享,该模型是模拟的煤层塌陷的pfc2
- Python 实现GA-RF遗传算法优化随机森林算法多输入单输出回归预测的详细项目实例(含完整的程序,GUI设计和代码详解)
- 电机模型、PI控制器与PLL锁相环的标幺化处理详解:从理论到实践,采样时间处理全解析,电机模型、PI控制器与PLL锁相环的标幺化处理详解:从理论到实践,采样时间处理全解析,电机标幺化、PI标幺化、锁相
- 基于西门子S7-1200PLC的现代化创新立体车库:传统与未来科技结合的简约程序与仿真图纸及新能源汽车充电解决方案,基于西门子S7-1200PLC的立体车库创新设计:融合新能源汽车充电功能,简约而不简
- Python 实现WOA-BP鲸鱼优化算法优化BP神经网络多输入单输出回归预测的详细项目实例(含完整的程序,GUI设计和代码详解)
- Python 实现SA-BP模拟退火算法优化BP神经网络多输入单输出回归预测的详细项目实例(含完整的程序,GUI设计和代码详解)
- HCIP-Datacom题库.zip
- Python 实现GA-ELM遗传算法优化极限学习机多输入单输出回归预测的详细项目实例(含完整的程序,GUI设计和代码详解)
- MinGW-w64安装指南.pdf
- Python 实现SA-ELM模拟退火算法优化极限学习机多输入单输出回归预测的详细项目实例(含完整的程序,GUI设计和代码详解)
- numpy-2.2.0-cp311-cp311-win_amd64.whl
- Python 实现DRN深度残差网络多输入分类预测的详细项目实例(含完整的程序,GUI设计和代码详解)
- PFC 5.0 流体与固体相互作用-流固耦合模型实战指南(实用干货版),PFC5.0流固耦合模型应用手册:干货满载的水力压裂与达西渗流常用案例集锦,该模型是“PFC2D流固耦合常用案例合集”: 其中
- Python 实现TSO-SVM金枪鱼群算法优化支持向量机多输入单输出回归预测的详细项目实例(含完整的程序,GUI设计和代码详解)
- Yoast SEO Premium v24.6 – WordPress SEO 插件 全功能版-20250306-134428.zip
资源上传下载、课程学习等过程中有任何疑问或建议,欢迎提出宝贵意见哦~我们会及时处理!
点击此处反馈


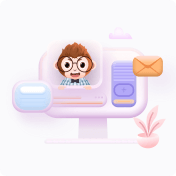