没有合适的资源?快使用搜索试试~ 我知道了~
Infineon-WhitePaper-Industrial-Battery-formation-WP
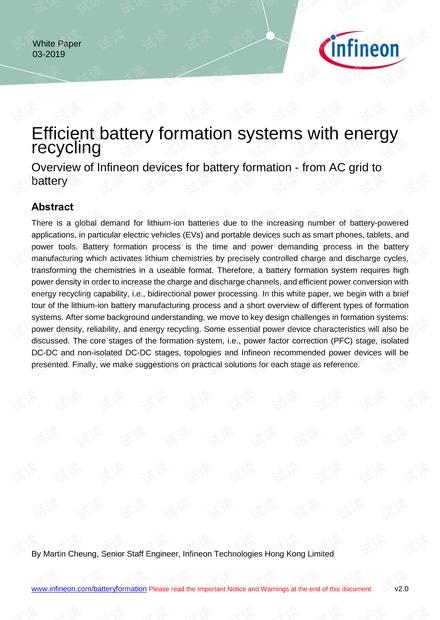

试读
21页
需积分: 0 0 下载量 47 浏览量
更新于2023-07-17
收藏 1.25MB PDF 举报
Infineon 白皮书 关于高效电池再生系统
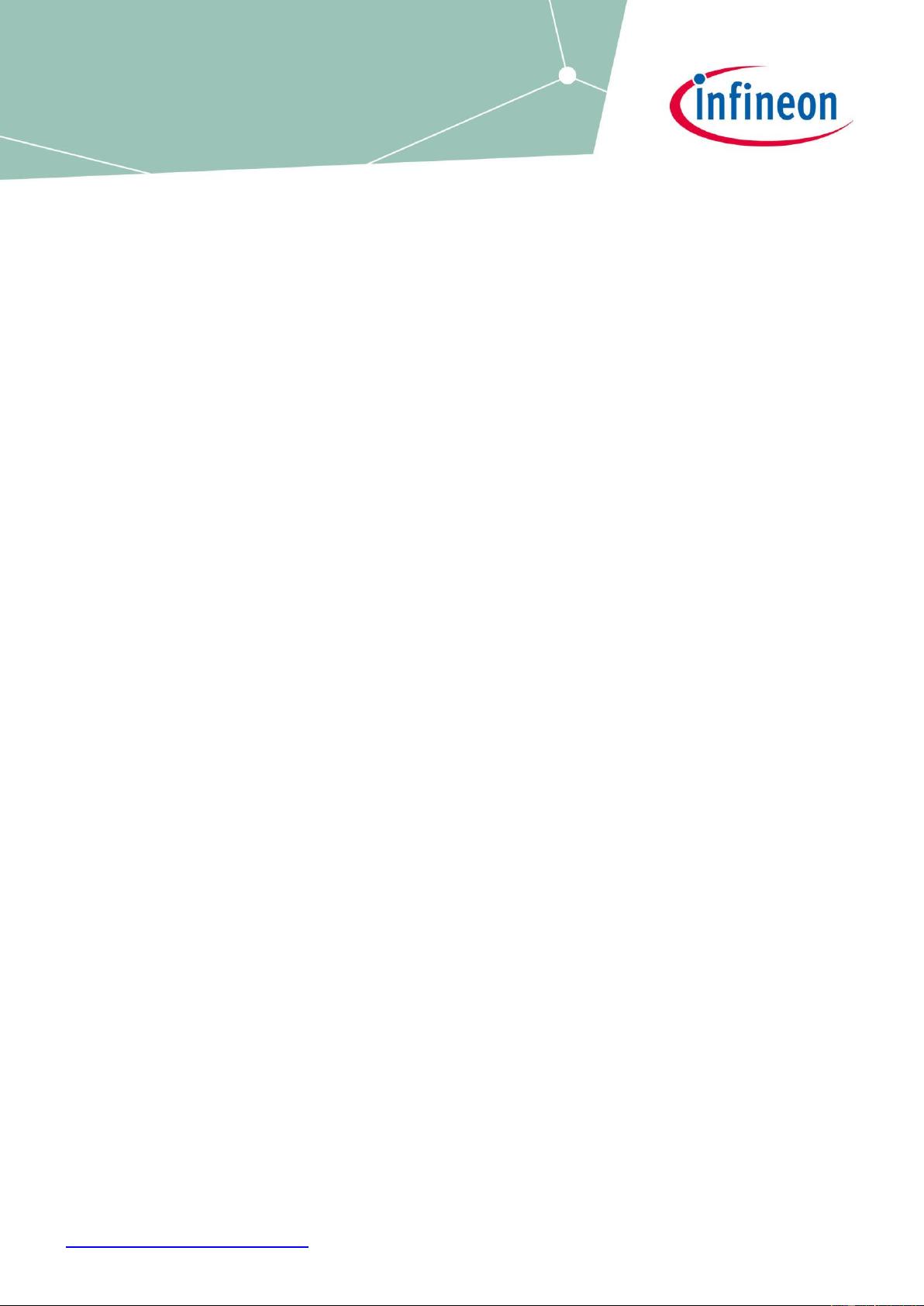
White Paper
03-2019
www.infineon.com/batteryformation Please read the Important Notice and Warnings at the end of this document v2.0
Efficient battery formation systems with energy
recycling
Overview of Infineon devices for battery formation - from AC grid to
battery
Abstract
There is a global demand for lithium-ion batteries due to the increasing number of battery-powered
applications, in particular electric vehicles (EVs) and portable devices such as smart phones, tablets, and
power tools. Battery formation process is the time and power demanding process in the battery
manufacturing which activates lithium chemistries by precisely controlled charge and discharge cycles,
transforming the chemistries in a useable format. Therefore, a battery formation system requires high
power density in order to increase the charge and discharge channels, and efficient power conversion with
energy recycling capability, i.e., bidirectional power processing. In this white paper, we begin with a brief
tour of the lithium-ion battery manufacturing process and a short overview of different types of formation
systems. After some background understanding, we move to key design challenges in formation systems:
power density, reliability, and energy recycling. Some essential power device characteristics will also be
discussed. The core stages of the formation system, i.e., power factor correction (PFC) stage, isolated
DC-DC and non-isolated DC-DC stages, topologies and Infineon recommended power devices will be
presented. Finally, we make suggestions on practical solutions for each stage as reference.
By Martin Cheung, Senior Staff Engineer, Infineon Technologies Hong Kong Limited
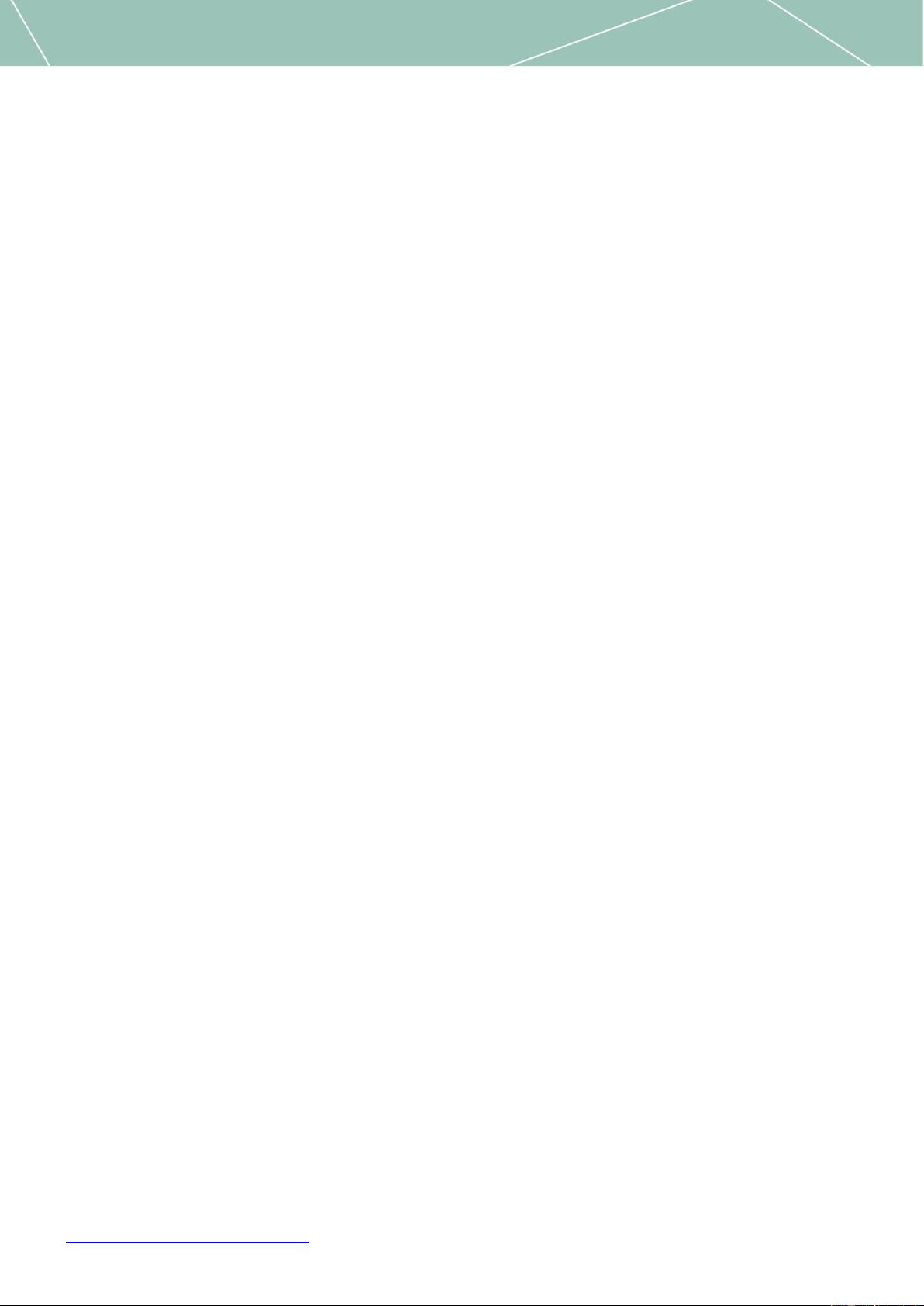
Efficient battery formation systems with energy recycling
Overview of Infineon devices for battery formation - from AC grid to battery
www.infineon.com/batteryformation 2
03-2019
Table of contents
1 Introduction to battery formation 3
1.1 What is battery formation? 3
1.2 Types of formation systems 4
2 System design challenges 7
3 Key topologies and Infineon device technologies 8
3.1 Unidirectional PFC converter 8
3.2 Bidirectional PFC converter 9
3.3 Isolated unidirectional DC-DC converter 10
3.4 Isolated bidirectional DC-DC converter 11
3.5 Non-isolated DC-DC converter 12
3.6 Auxiliary circuit and driver ICs in the system 12
4 Recommendation of Infineon devices and demonstration boards 14
4.1 Power factor correction converter 14
4.2 Isolated DC-DC converter 15
4.3 Non-isolated DC-DC converter 16
5 Summary 18
References 19
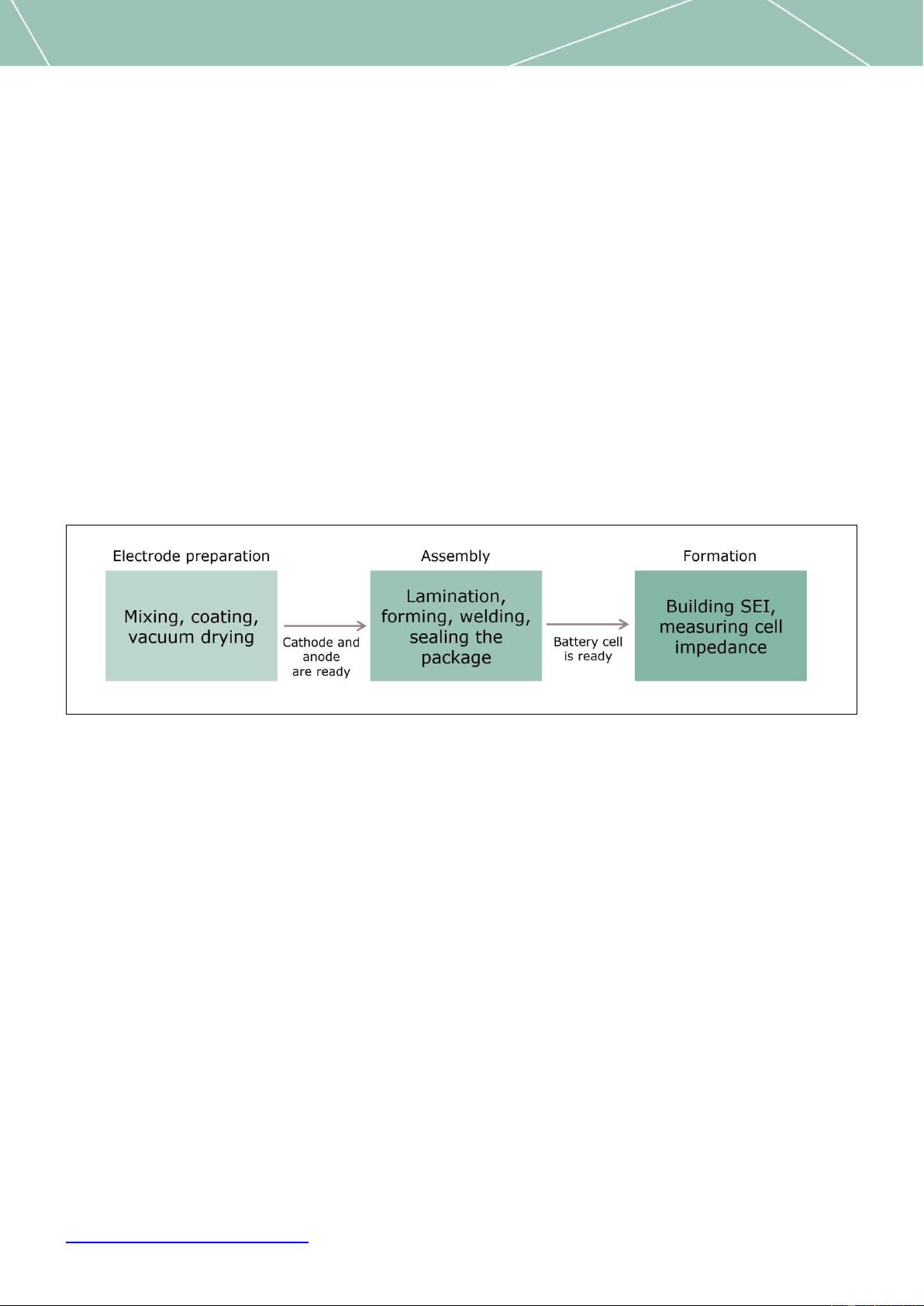
Efficient battery formation systems with energy recycling
Overview of Infineon devices for battery formation - from AC grid to battery
www.infineon.com/batteryformation 3
03-2019
1 Introduction to battery formation
Our everyday lifestyle trends towards having more and more wireless and battery powered devices in our
surroundings. The worldwide battery production capacity is estimated to increase substantially year by
year. This trend is driven by the growing demand of battery powered devices and the rapidly rising number
of EVs, targeting high capacity batteries of 500-700 watt-hour per kg. The essential stage every battery
needs to undergo in the manufacturing process is called battery formation [1]. The purpose of battery
formation is to activate battery chemistries and also to determine the characteristic of the battery [2]. In
this process, every newly assembled battery is initially charged and discharged with high accuracy.
Nowadays, battery formation is the bottleneck of battery production due to the fact that it can take up to
several days or even weeks depending on the cell manufacturer and cell chemistry [3-4]. It also has a
great impact on battery lifetime [2], quality, and cost [4].
1.1 What is battery formation?
Figure 1 A simplified scheme of the lithium-ion battery manufacturing process
Figure 1 shows the lithium-ion battery manufacturing process that includes electrode preparation,
assembly, and formation. The battery formation stage has two key functions; on one hand to create the
solid electrolyte interphase (SEI) on the anode and cathode electrolyte interphase (CEI) [1-2]. On the other
hand, during the formation process battery cell performance measurements, such as impedance and
current capacity, are collected and recorded for battery pack process or quality analysis. SEI and CEI
layers are created by deposition in the formation process when the cells take their first charge. Since the
electrolyte lithium salt dissolved in organic solvent, it reacts vigorously with carbon anode during the initial
formation charge and builds a thin SEI layer by the moderated charge rate with 0.1 C rated current.
1 C rate means that the discharge current will discharge the entire battery in one hour. To complete the
formation process, 3-5 cycles at 0.1 C at room temperature and 3-5 cycles at higher C-rate at higher
temperature are required [3] to control the thickness of the SEI layer. This takes several days and means
the bottleneck in the battery formation process and the battery production itself. The thick SEI layer
increases the internal impedance of the battery, which reduces current capability and decreases charging
and discharging cycle times [2]. Unlike the battery standard charging procedures, battery formation
process begins with a low current, 0.1 C [3], and variable output voltage which requires the reliable battery
formation power supply to provide stable charging and discharging current.
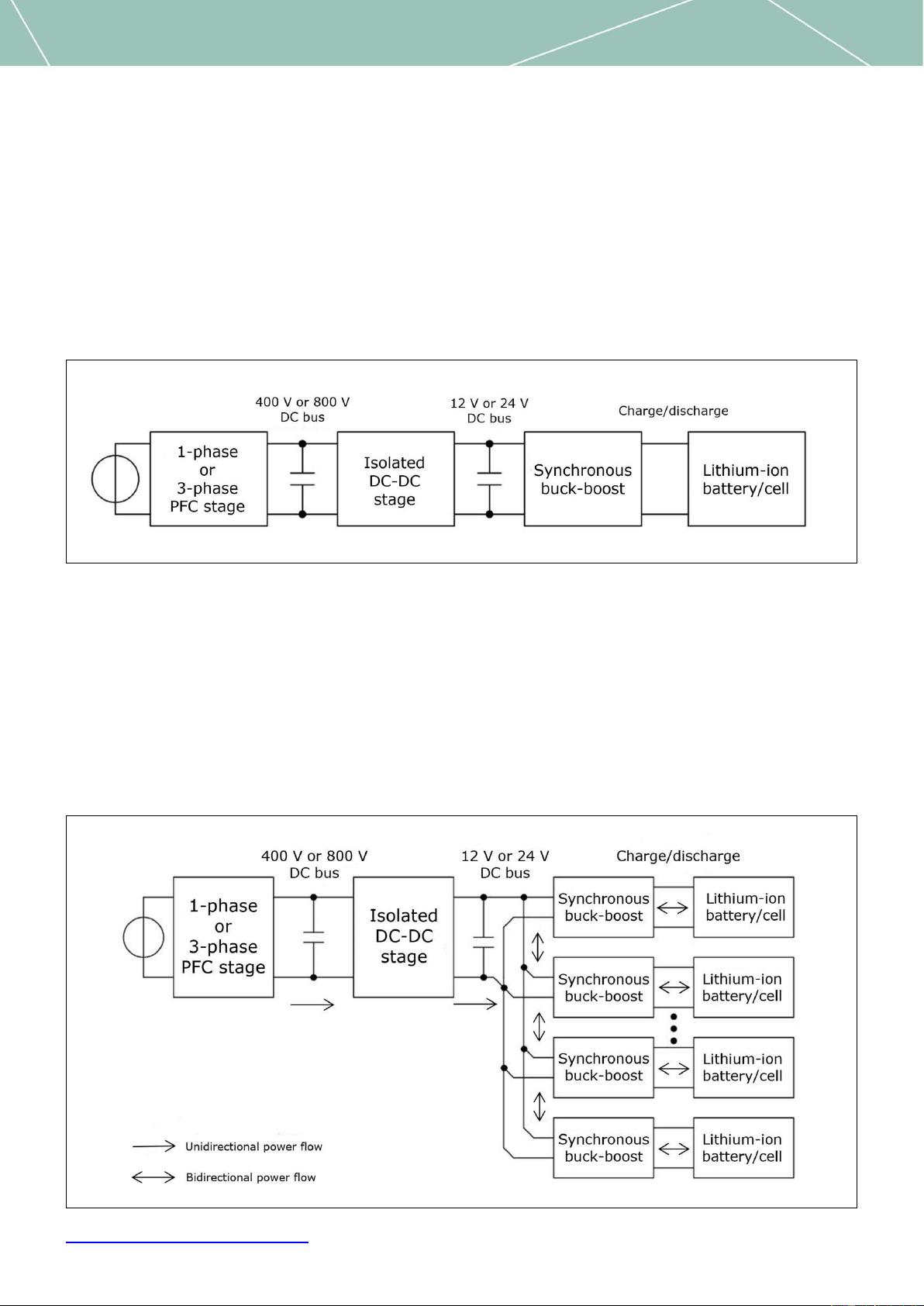
Efficient battery formation systems with energy recycling
Overview of Infineon devices for battery formation - from AC grid to battery
www.infineon.com/batteryformation 4
03-2019
1.2 Types of formation systems
Figure 2 shows the functional block diagram of the formation of the power supply from the AC grid to the
formatted battery. As depicted, the system includes a PFC stage as an interface to the AC grid, an isolated
DC-DC stage for galvanic isolation and voltage step down, and a non-isolated DC-DC stage to provide
tight charge and discharge voltage together with well-controlled charge and discharge current. All the
stages are based on switching converter technologies rather than linear regulators. The switching
converter approach allows the formation system to increase energy efficiency, power density, and gives
the possibility to use the same hardware for energy recycling, thus reducing battery manufacturing cost.
Figure 2 Basic block diagram for battery formation switching mode power supply
Figures 3, 4 and 5 show different types of energy recycling formation systems in which the isolated DC-
DC converter usually supports more than one channel in the non-isolated DC-DC converter for battery cell
formation. The traditional and simple switching converter approach uses synchronous (SR) buck-boost
converter for bidirectional power flow. The PFC stage and the isolated DC-DC stage have unidirectional
power flow from the AC grid to the buck-boost input as shown in Figure 3. This energy recycling is based
on controlling the charging and discharging time of each or a set of buck-boost converters, therefore the
discharging energy may cannot be completely recycled.
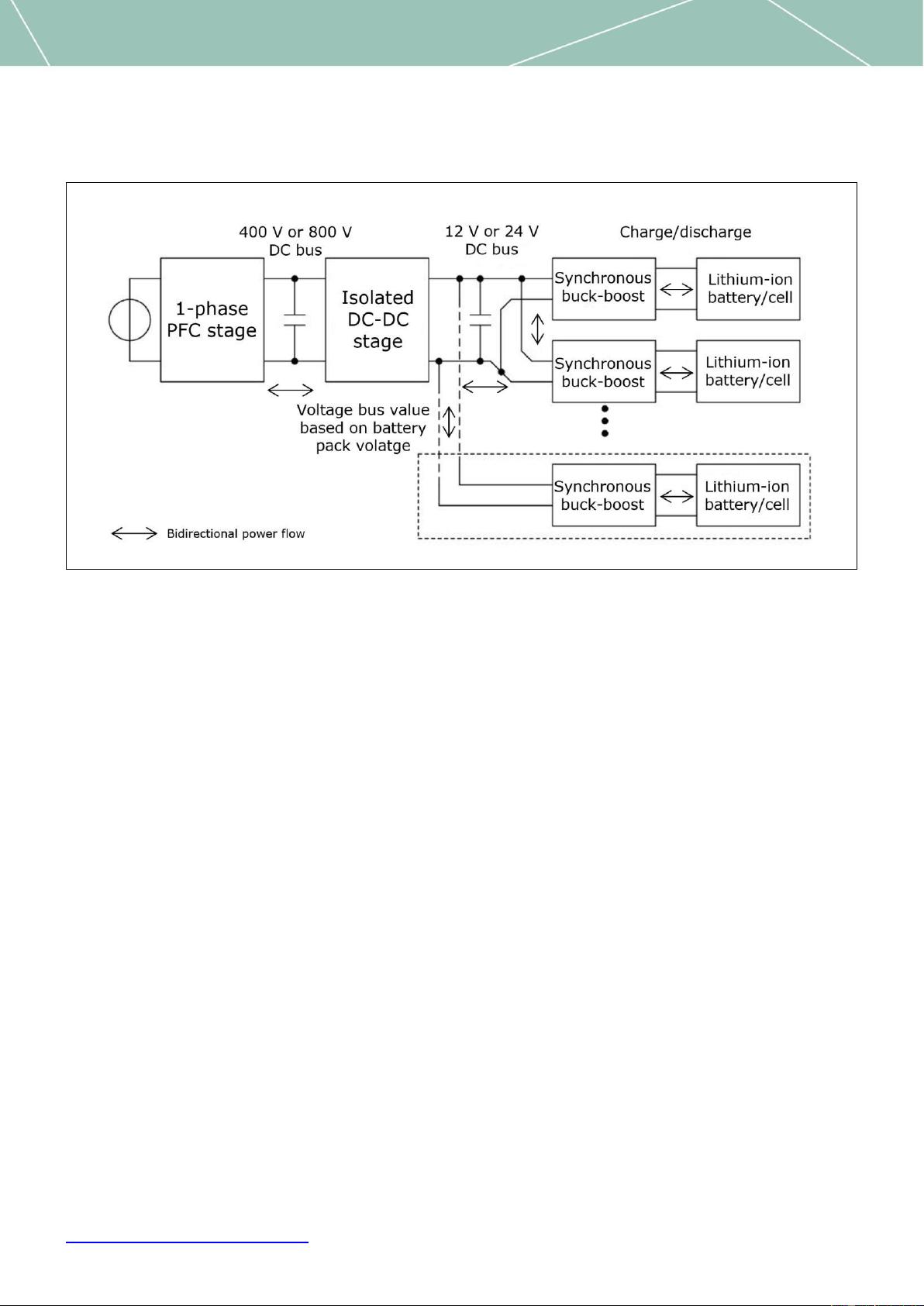
Efficient battery formation systems with energy recycling
Overview of Infineon devices for battery formation - from AC grid to battery
www.infineon.com/batteryformation 5
03-2019
Figure 3 Simple approach for limited energy recycling at the non-isolated buck-boost stage
Figure 4 Bidirectional battery formation system energy recycling from battery to the AC grid
A full bidirectional energy flow battery formation system is shown in Figure 4. Compared to the traditional
approach, the discharge energy can transfer from the formatted batteries to the grid due bidirectional
power flow design of the isolated DC-DC and the PFC stages. The system’s charge and discharge power
level is usually a few kilowatts and the connected buck-boost converters should charge and discharge at
the same time to maximize recycling energy efficiency. This configuration allows to measure the high
power battery pack characteristics, but designing the isolated DC-DC stage is required to provide a certain
range of variable output voltages.
剩余20页未读,继续阅读
资源推荐
资源评论
168 浏览量
2021-09-30 上传

201 浏览量

147 浏览量
2022-07-14 上传
2022-02-08 上传
2022-07-14 上传
142 浏览量
2021-09-30 上传
2022-07-14 上传
141 浏览量
172 浏览量
2021-06-17 上传
160 浏览量
116 浏览量
128 浏览量
116 浏览量
178 浏览量
106 浏览量
2021-03-18 上传

190 浏览量

资源评论
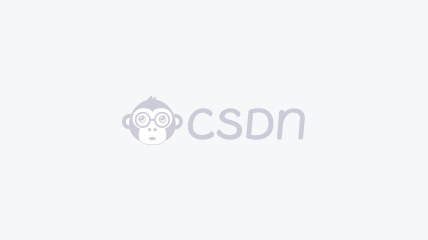

k_str
- 粉丝: 0
- 资源: 5
上传资源 快速赚钱
我的内容管理 展开
我的资源 快来上传第一个资源
我的收益
登录查看自己的收益我的积分 登录查看自己的积分
我的C币 登录后查看C币余额
我的收藏
我的下载
下载帮助

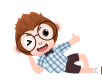
最新资源
- 【微信小程序源码】京东首页demo
- 《大闹天宫》动画美术风格中的中国传统元素分析_张星辉.caj
- VCU Simulink需求与功能开发文档:集成档位控制、ON Start启动、上下电管理、扭矩调控、能量优化与滑行回收的全方位控制系统需求说明,VCU Simulink需求与功能开发文档:集成档位控
- 基于COMSOL Multiphysics的三维岩石酸化过程模拟:探讨酸液在碳酸盐岩储层中的流动、传质与反应机制,利用COMSOL Multiphysics模拟三维岩石酸化过程:探讨酸液在碳酸盐岩储层
- 台达DVP PLC与西门子V20变频器通讯程序:可靠控制,自动化调整,接线与设置指南,台达DVP PLC与西门子V20变频器通讯程序:可靠控制,自动化调整,接线与设置指南,台达DVP PLC与3台西门
- 基于Python的Django-vue基于大数据的学习资源推送系统实现源码-说明文档-演示视频.zip
- PHP API 客户端,可让您与 deepseek API 进行交互 deepseek-php-client-2.0.3
- 【微信小程序源码】和茶网
- 自然启发MPPT优化技术,霜冰优化算法RIME在MPPT中对光伏局部遮阴情况的性能提升研究,霜冰算法RIME优化mppt,光伏mppt , 局部遮阴光伏mppt 2023年,H Su等人受到自然界霜冰
- 使用 PHP Deepseek 实现问答 ask-deepseek
- COMSOL Multiphysics中的comsol支架静态分析:基本原理、操作与结果分析,COMSOL Multiphysics中的comsol支架静态分析:基本原理、操作与结果分析,comsol
- 基于Python的Django-vue基于大数据的银行信用卡用户的数仓系统源码-说明文档-演示视频.zip
- 翱捷功能机常见空间问题的解决
- 西门子博途1500双驱同步编程实例分享,结构化编程、伺服同步运行、多用户权限登录,开发者必备的学习参考(版本v16),西门子博途V16全新双驱同步与三轴码垛程序:结构化编程框架,多用户权限控制,高值学
- DotSpatial库学习
- Delphi 12.5 控件之delphi实现腾讯签名算算法源代码.rar
安全验证
文档复制为VIP权益,开通VIP直接复制
