
数据资源
- 粉丝: 146
- 资源: 23万+
最新资源
- 基于Jupyter Notebook的AI学习理论与应用实战源码
- 基于高频信号注入的三相永磁同步电机无传感器控制与Matlab仿真研究,基于高频信号注入的三相永磁同步电机无传感器控制与Matlab仿真研究,基于高频信号注入的三相永磁同步电机无传感器控制仿真;旋转电压
- 三次B样条优化:独立子程序,适用于所有Matlab程序,直接优化使用指南,三次B样条优化独立子程序,适用于所有Matlab程序,一键提升程序性能,3次B样条优化,适用于所有matlab程序,单独的独立
- 基于主从博弈与粒子群算法的电热综合能源系统动态定价与能量管理优化模型,基于主从博弈的电热综合能源系统动态定价策略与能量管理优化模型研究-MATLAB实现与CPLEX求解器应用,MATLAB代码:基于
- 基于Cruise软件的增程混动仿真模型:功率跟随控制策略详解与串联混动汽车动力经济性仿真探究,基于Cruise软件的增程混动仿真模型:功率跟随控制策略详解与串联混动汽车动力经济性仿真探究,cruise
- 日前日内两阶段调度综合能源分析:基于Matlab与Yalmip的优化结果对比及机组成本与弃风惩罚的探讨,日前日内两阶段调度综合能源分析:基于Matlab与Yalmip的优化结果对比及机组成本与弃风惩罚
- 西门子新能源四轴自动排列机:基于RFID与MES通讯的V90控制程序,详细注释与CAD电气图,适合初学者进阶参考,西门子新能源四轴自动排列机V14全解析:轴控制、RFID读写与MES通讯全攻略,西门子
- 基于Html+JavaScript的结婚请柬设计源码示例demo
- 日前日内两阶段调度综合能源分析:基于Matlab与Yalmip的程序优化结果对比及成本考量,基于Matlab与Yalmip编程的综合能源调度策略对比:考虑需求响应与弃风惩罚的日前日内两阶段调度研究,日
- C# Windows窗口开发实战:图书管理系统的设计与实现,包括详细文档介绍,基于C#的Windows窗口图书管理系统:功能介绍与文档指南,C# Windows窗口,图书管理系统 包含文档介绍 ,C#
- 三菱FX3U与两台变频器Modbus RTU通讯CRC程序详解:实现正反转控制、频率读写及电压电流监控,三菱FX3U与两台变频器Modbus RTU通讯CRC程序详解:控制正反转、频率写入与读取、电压
- 《自研电动汽车永磁电机后驱模型:8极48槽配置与性能分析手册》,电动汽车永磁电机后驱模型:搭建、性能分析与效率优化,某整车厂电动汽车永磁电机后驱模型,8极48槽配合,自己一手搭建,可以分析出电机基本性
- 西门子1200脉冲运动控制块:便捷调用,多种功能,博途西门子v15以上兼容,省心高效实现轴控制,西门子1200脉冲运动控制块:高效便捷,实现多种运动模式与轻松调试,适用于博途西门子v15及以上版本,西
- 基于Python技术的社区医疗老年人体检项目设计源码
- 燃料电池多点恒功率工作Cruise与Matlab联合仿真模型介绍及功能实现,燃料电池多点恒功率工作Cruise仿真模型的设计与实现(基于Cruise 2019与Matlab Simulink联合开发)
- 基于纳什谈判理论的风-光-氢多主体能源系统协同合作运行仿真方法研究,基于纳什谈判理论的风光氢多主体能源系统协同运行策略MATLAB实现,MATLAB代码:基于纳什谈判理论的风–光–氢多主体能源系统合作
资源上传下载、课程学习等过程中有任何疑问或建议,欢迎提出宝贵意见哦~我们会及时处理!
点击此处反馈


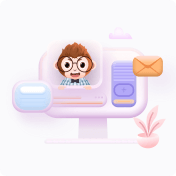