本文探讨了在某铜矿中实施自动化系统于高效节能碎磨系统中的应用实践。主要涉及了该铜矿碎矿工段的过程自动控制系统构建、优化控制平台的实施,以及实现生产过程自动化、控制智能化的具体措施。通过自动化控制系统的应用,实现了集中监控碎矿生产过程,并通过终端掌握整个工段的运行状态,达到了降低人力成本、维持产量,并保留扩展空间以便后期升级和优化的目的。 关键词中的“超细碎”指的是在选矿过程中对矿石进行超细破碎处理,以保证系统产品粒级和分布率的稳定性。超细碎系统一般由皮带机、高压辊、直线振动筛、渣浆泵等设备构成。其运行效果的重要参数包括筛分后矿浆的粒级和分布,这些效果受原矿性质、高压辊的工作效率和直线振动筛的工作状况等因素影响。 文中提到的“自寻的给矿控制方案”是将需要控制的参数进行解耦,分别控制给矿量、给水量、进筛分矿浆的浓度、渣浆泵的工作频率等,并且根据矿石性质和碎矿条件的变化,采用了三种控制策略:恒定给矿自动控制系统、考虑矿石性质变化的自动控制系统以及自寻的自动控制系统。自寻的给矿控制系统主要利用称重传感器作为检测元件,执行机构为可开度控制的料仓口与带变频器的胶带机,控制单元采用PLC(可编程逻辑控制器)。 在工艺流程方面,矿石经过破中破后分别进入多个具有可调开度功能的原粉矿胶带机,并通过振动给料机进入集矿胶带机;再由胶带机转运至高压辊称重料仓,经高压辊磨机超细碎后进入分矿溜槽直至直线振动筛,筛上产品再次进入高压辊破碎或打散,筛下产品则由渣浆泵送至球磨溢流矿浆池,最终通过砂浆泵、旋流器进入球磨系统。 在自动化改造的过程中,矿石的处理流程中涉及的各个设备,如高压辊、直线振动筛、渣浆泵等均被纳入了监控单元,实现了对它们的关键参数的实时监控和控制,以维持高效稳定的生产效率和产品质量。例如,高压辊磨机采用层压粉碎原理,通过液压系统和给料系统对工作辊进行驱动,并利用PLC系统实现转速的自整定和控制。 此外,为了保证直线振动筛筛分的稳定性,还实施了分段控制策略,使用超声波液位计测量液位,并送入PLC系统中进行精确控制。通过设置液位值的上下限、警戒线等参数,结合实际生产情况,调整水压控制策略,确保筛分效果和矿浆浓度的稳定性。 综合以上内容,我们可以看到,在铜矿的碎磨系统中,引入自动化系统是一个涉及到工艺流程重构、设备优化配置、智能监控与控制技术集成的复杂工程。它不仅需要对现场情况进行详细分析,还需选择适合的技术路线和设备配置,实现设备智能化、生产过程自动化和监控集中化。通过这些措施,能够有效提升铜矿的生产效率,降低能耗和人力成本,同时也为后续的生产管理和技术升级留有充分的余地。
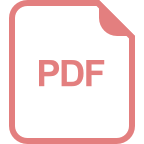
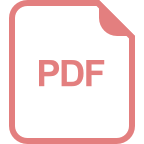
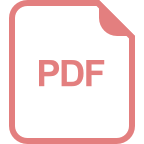
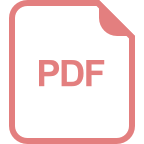
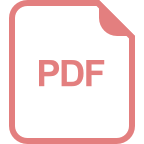
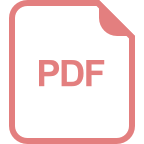
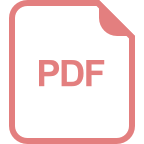
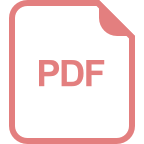
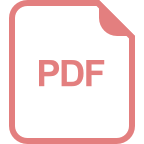
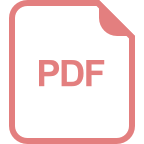
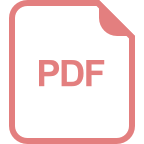
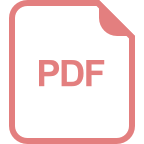
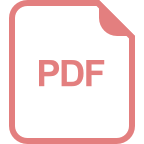
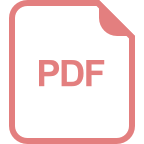
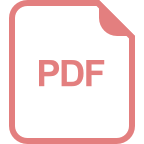
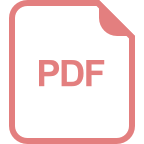
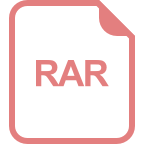
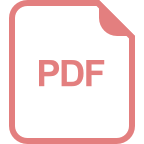
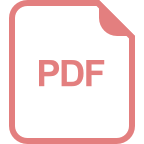
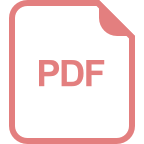
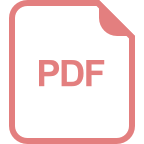
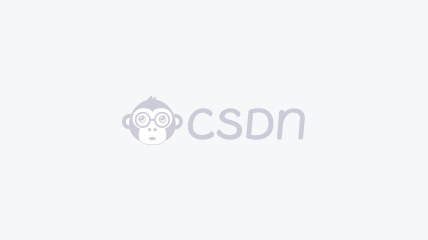

- 粉丝: 133
- 资源: 23万+





我的内容管理 展开
我的资源 快来上传第一个资源
我的收益
登录查看自己的收益我的积分 登录查看自己的积分
我的C币 登录后查看C币余额
我的收藏
我的下载
下载帮助

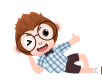
最新资源

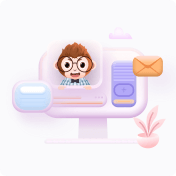
