
数据资源
- 粉丝: 136
- 资源: 23万+
最新资源
- 基于ThinkPHP的投资分析、真实模拟平台详细文档+全部资料+高分项目.zip
- 基于Vue2.x的记账单记录、账单分析系统详细文档+全部资料+高分项目.zip
- 基于vnpy,支持多账户,多策略,实盘交易,数据分析,分布式在线回测,风险管理,多交易节点的量化交易系统;支持CTP期货,股票,期权,数字货币等金融产品详细文档+全部资料+高分项目.zip
- 基于百度识别API的客流分析统计系统详细文档+全部资料+高分项目.zip
- 基于成交量的股票数据分析系统详细文档+全部资料+高分项目.zip
- 基于大学生课程成绩挖掘分析的就业预测系统详细文档+全部资料+高分项目.zip
- 基于多通道卷积神经网络的汽车评论情感分析系统详细文档+全部资料+高分项目.zip
- 基于混沌系统和DNA编码的彩色数字图像加密、解密、抗噪声性能分析以及抗裁剪性能分析详细文档+全部资料+高分项目.zip
- 基于时间指数的股票价值分析系统详细文档+全部资料+高分项目.zip
- 基于计算机视觉,路面分析,及交通路况识别的车辆辅助驾驶系统详细文档+全部资料+高分项目.zip
- 基于微博的网络舆情话题分析和用户画像系统详细文档+全部资料+高分项目.zip
- 基于知识库的问答系统、其中使用带注意力机制的对抗迁移学习做中文命名实体识别,使用BERT模型做句子相似度分析。详细文档+全部资料+高分项目.zip
- 四足机器狗模型3D图纸和工程图机械结构设计图纸和其它技术资料和技术方案非常好100%好用.zip
- 毕业设计-基于智慧景区之PC端(管理端)后台管理系统全部资料+高分项目+详细文档.zip
- 基于CS架构的武汉市智慧旅游系统iTravel全部资料+高分项目+详细文档.zip
- 基于PaddlePaddle的智慧课堂实时监测系统全部资料+高分项目+详细文档.zip
资源上传下载、课程学习等过程中有任何疑问或建议,欢迎提出宝贵意见哦~我们会及时处理!
点击此处反馈


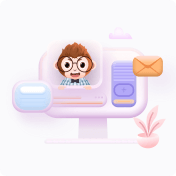