
数据资源
- 粉丝: 138
- 资源: 23万+
最新资源
- MATLAB代码:基于改进K-means算法的含电动汽车负荷源荷场景聚类 关键词:有序聚类 改进k-means聚类 电动汽车负荷聚类 风光场景聚类 仿真平台:MATLAB 主要内容:代码主要做的
- Matlab基于POA-LSSVM鹈鹕算法优化最小二乘支持向量机的数据多输入单输出回归预测(含完整的程序,GUI设计和代码详解)
- MATLAB 实现基于长短期记忆网络(LSTM)进行时间序列预测模型的项目详细实例(含完整的程序,GUI设计和代码详解)
- 八自由度车辆动力学Simulink仿真模型 模型包括.slx文件.m车辆参数文件和word说明文档 Matlab版本2018a,可生成低版本 八自由度包括纵向,横向,横摆,侧倾及四个车轮旋转运动,另外
- 毕设基于Dlib和OpenCV的人脸识别考勤系统设计与实现(python源码+数据库).zip
- 葡萄酒质量数据集,葡萄酒品质数据集(包含21,000条记录和12个变量)
- 电网+图像样本+voc格式
- MATLAB代码:基于遗传算法的风电混合储能容量优化配置 关键词:混合储能 容量配置优化 遗传算法 参考文档:《基于遗传算法的风电混合储能容量优化配置》无超级电容器 ; 仿真平台:MATLAB
- javascript为了在前面插入一个新节点,我们创建一个新节点并将其下一个引用指向
- 基于python+OpenCV人脸识别系统设计与实现.docx
- MATLAB代码:含多种需求响应及电动汽车的微网 电厂日前优化调度 关键词:需求响应 空调负荷 电动汽车 微网优化调度 电厂调度 参考文档:计及电动汽车和需求响应的多类电力市场下电厂竞标模型
- javascript在链表中的给定节点之前插入一个节点
- 基于Matlab实现ASK、FSK、PSK仿真包括信号产生,调制,加噪声,解调和还原信号误码率分析(源码+数据).rar
- 转矩补偿,振动、谐振抑制 可用于实际项目… matlab二质量模型… 使用巴特沃斯高通滤波器提取转速波动进行转矩补偿,实现主动阻尼 加速度反馈: 等效增加电机惯量 提供详实文档、仿真模型… 效果如图
- 汇川H5U-EtherCAT四轴定位,其中两轴联动做矩形涂胶 显示屏涂胶机 1.主cpu汇川H5U搭载四个汇川ISV6系列总线伺服驱动器,进行运动控制,单轴控制,双轴联动控制 2.汇川IT7000系
- 金融机构数据集,银行数据集,金融数据,全球最大的金融机构(银行业、保险业、金融集团等)的综合概览(数据集包括重要的财务指标,例如收入、净利润和总资产)
资源上传下载、课程学习等过程中有任何疑问或建议,欢迎提出宝贵意见哦~我们会及时处理!
点击此处反馈


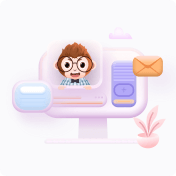