
数据资源
- 粉丝: 138
- 资源: 23万+
最新资源
- 【岗位职责说明书】100000817 财务主管.doc
- 【岗位职责说明书】100000824 安全保卫主管.doc
- 【岗位职责说明书】100000825 退休人员管理主管.doc
- 【竞业禁止】-03-股东竞业禁止协议范本.docx
- 【竞业禁止】-04-竞业禁止范本【律师备注,含风险提示】.doc
- 【竞业限制】-01-竞业限制协议【律师备注,风险提示】.doc
- 【竞业限制】-03-竞业限制协议【通用版本】.doc
- 【竞业限制】-02-竞业限制协议【通用版本】.docx
- 【竞业限制】-05-播竞业限制协议【简洁版】.docx
- 【竞业限制】-06-主播竞业限制协议【详细版】.docx
- 深度学习注意力机制: 工作原理、类型及其应用
- 【保密协议】-00-员工保密协议【律师拟定,风险提示】.doc
- 【保密协议】-06-员工保密协议【适合普通员工】.doc
- 【保密协议】-02-股东保密协议【适合公司股东】.doc
- 【保密协议】-07-员工保密协议【适合销售人员】.doc
- 【保密协议】-03-员工保密协议【适合中高层管理者,含承诺书】.docx
资源上传下载、课程学习等过程中有任何疑问或建议,欢迎提出宝贵意见哦~我们会及时处理!
点击此处反馈


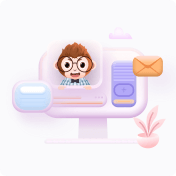