
数据资源
- 粉丝: 150
- 资源: 23万+
最新资源
- 2015-2024年上市公司商道融绿esg评级数据(年度)
- DeepSeek:通用人工智能从入门到精通的技术解析与应用指南
- 离散扩展龙伯格观测器:扰动补偿功能下的鲁棒性能优化及动态响应增强策略,离散扩展龙伯格观测器:具有扰动补偿功能的高鲁棒性预测控制系统,一种具有扰动补偿功能的离散扩展龙伯格观测器,有较好的参数摄动扰动抑制
- 无刷直流电机BLDC三闭环控制系统的Matlab Simulink仿真模型搭建:原理、波形记录与参数详解,无刷直流电机BLDC三闭环控制系统的Matlab Simulink仿真模型搭建:原理、波形记录
- 基于Python的Django-vue基于spark的短视频推荐系统的设计与实现源码-说明文档-演示视频.zip
- DeepSeek写的重力球迷宫手机小游戏
- 单相变压器绕组与铁芯振动形变仿真模型:洛伦兹力与磁致伸缩效应下的动态响应分析,COMSOL单相变压器绕组与铁芯振动形变仿真模型:基于洛伦兹力与磁致伸缩效应的时域分析,comsol的单相变压器绕组及铁芯
- 新兴经济体二氧化碳排放报告2024.pdf
- 激光熔覆技术:COMSOL模拟建模与视频教程服务,助力激光研究人员与工程师的专业提升,激光熔覆技术:COMSOL软件下的建模与视频教程应用指南,COMSOL 激光 激光熔覆 名称:激光熔覆 适用人群:
- 2000-2023年上市公司价值链升级数据(含原始数据+计算代码+结果)
- COMSOL仿真下的钢架无损超声检测:焊接区域及周边缺陷识别技术,角钢梁纵波转横波检测原理揭秘,Comsol仿真技术下的钢架无损超声检测:角钢梁缺陷的精准识别与定位,Comsol仿真钢架无损超声检测
- 基于FPGA的图像坏点像素修复算法实现及Matlab辅助验证:探索其原理、测试与使用视频教程 注:标题中的“可刀”一词在此上下文中并无实际意义,因此未被包含在标题中 标题长度符合要求,并尽量简洁明了
- 2008-2022年各省环境污染指数数据(原始数据+结果).xlsx
- zhaopin_mzhan.apk
- 权威科研机构发布钢轨表面缺陷检测数据集,含400张图像和8种类别缺陷,mAP达0.8,附赠lunwen,钢轨表面缺陷检测数据集:包含400张图片与八种缺陷类别,适用于目标检测算法训练与研究 ,钢轨表面
- C形永磁辅助同步磁阻电机Maxwell参数化模型:转子手绘设计及关键参数优化分析,基于Maxwell参数化模型的C形永磁辅助同步磁阻电机研究:转子手绘非UDP模块的参数化设计及优化分析,C形永磁辅助同
资源上传下载、课程学习等过程中有任何疑问或建议,欢迎提出宝贵意见哦~我们会及时处理!
点击此处反馈


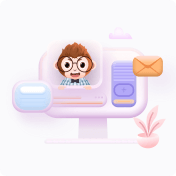