
数据资源
- 粉丝: 150
- 资源: 23万+
最新资源
- 时间戳同步方式讲解,message-filter 互斥锁 以及融合队列
- docker-compose搭建一整套前、后端分离系统部署涉及到mysql5.7、mysql8.0,nginx1.23、redis6、vue、jar包(springboot)
- 基于自监督三维语义表示学习的视觉语言导航
- sqlcipher连接工具(windows)
- 华为AP8050DN胖固件
- OfficeAI助手是一款免费的智能AI办公工具软件,专为MicrosoftOffice和WPS用户打造
- C语言从0到1教程包含源码和案例
- 台达DVP PLC与多台变频器通讯编程详解:昆仑通态接线方式与设置指南,实现频率设定、启停控制和状态读取指示功能,台达DVP PLC与3台台达VFD-M变频器通讯程序 实现频率设定、启停控制与状态读取
- 资源获取工具分享(轻松获取文档、小说、音乐、视频资源)
- vue3-element-template
- 基于go语言的GUI框架fyne开发的俄罗斯方块游戏
- 电子商务_前后端分离_管理系统_毕业设计_1740825497.zip
- 电子科技_本科论文_LaTex模板_1740825154.zip
- 电子科技大学本科毕设论文_LaTeX模板_1740824992.zip
- 计算机电子商城管理技术_用户购物体验提升系统_1740825257.zip
- 电子桌牌项目.zip
资源上传下载、课程学习等过程中有任何疑问或建议,欢迎提出宝贵意见哦~我们会及时处理!
点击此处反馈


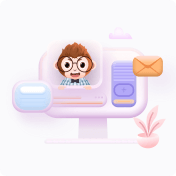