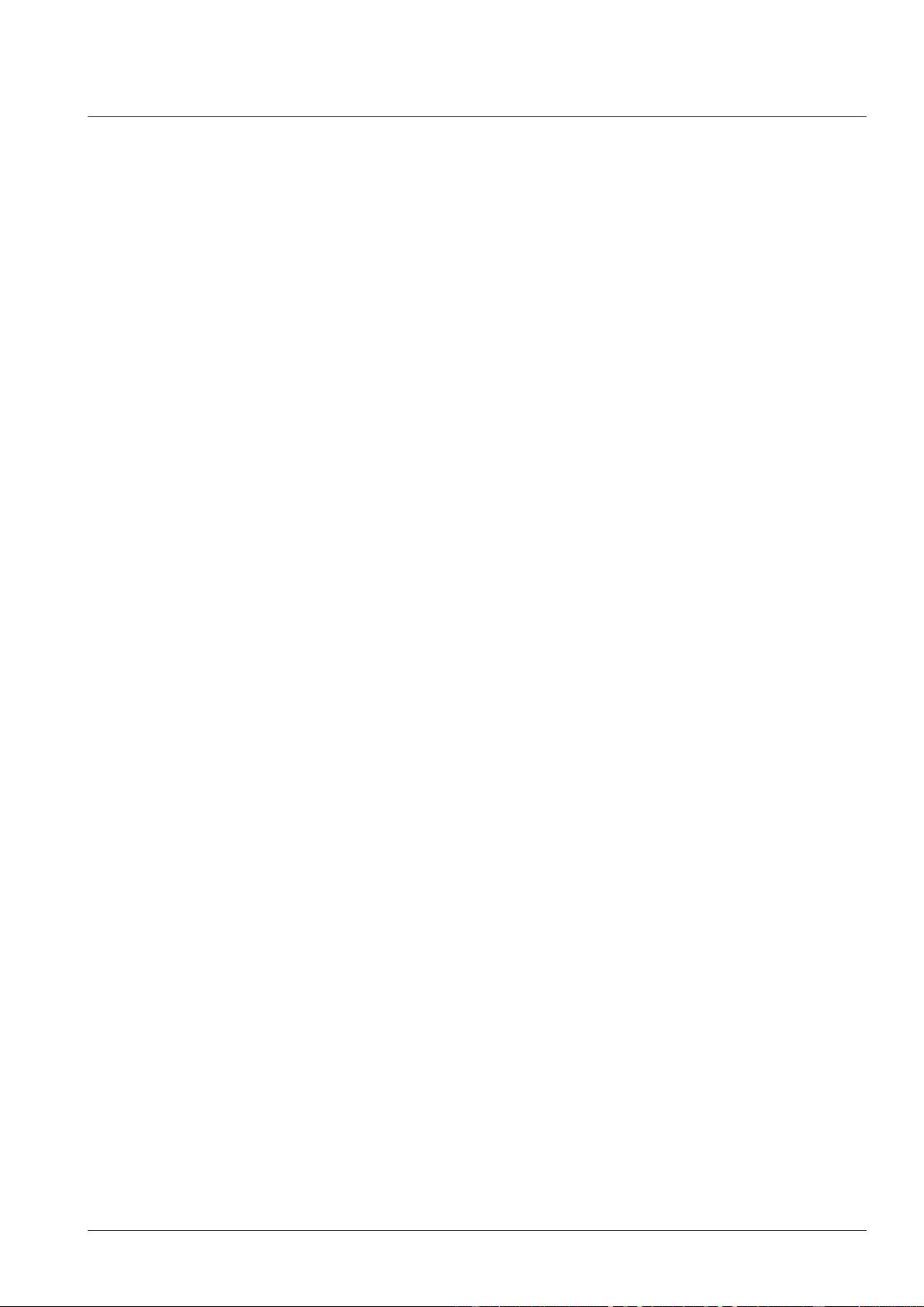
an equivalence ratio less than half of the normal
flammability limit was obtained with a subsequent
maximum gas temperature less than 1800 K leading
to a negligible NO
x
emission. Lloyd and Weinberg
[24] developed a spiral-shaped burner of high-
temperature metal alloys. A low-heat-content pre-
mixed mixture could be combusted by transferring
heat to the reactants whereas flowing to the centre
of the turns where a combustion bed was located.
Mixtures of fuel content corresponding to one-third
of the normal limit of flammability could be com-
busted. Moreover, Kesting and Trimis [25] reported
a stable combustion at an excess air factor as high
as 2.7 and the flame speed was found to be about
8–10 times higher than for the free flames.
Takeno et al. [26–29] performed a series of experi-
ments and analytical work. They found that the mass
burning flow rate does not rema in an eigenvalue, but
becomes a parameter influencing the flame location,
the heat recirculation, and the radiation output.
Changing the internal flame structure could be
achieved by inserting a solid into the flame zone.
The extent of the excess enthalpy may be controlled
by varying the solid porosity to alter the heat transfer
coefficient between the solid and the gas. Doubling
the solid length increased the critical maximum
mass flow rate about twice as much, where the tempe-
rature peak became sharper with a concentrated
reaction rate. Their results led to the consideration
of the heat loss as a parameter. In this sense, as the
flow rate increases, the heat loss becomes less
important relative to the gene rated heat, which in
turn allows extended stable flow rates. The latter con-
clusion highlights that porous burners exhibit their
salient features at relatively high firing rates, where
conventional burners’ flames could not be stabilized
at the corresponding flow velocities. Furthermore, in
porous burners the turbulence effects on both the
flame propagation and heat transfer enhance the
two-phase interaction (as discussed later). It was
referred to porous burners as systems with a constant
temperature flame, where the extended reaction
zone increases the reaction time at high flow vel-
ocities to reach the same flame temperature. Such a
conclusion impl ied that flame location inside the
porous matrix results in a mutual interference
between flame stability, gas, and solid temperatures
in the extended flame preheating zone.
The merits of the porous burners’ intense radiation
output, as coupled to a lean op eration, are mani-
fested by the less fuel consump tion at the same
output of burners, utilized as heating units. Echigo
et al. [11] found a reduction in the fuel consumption
by 60 per cent upon the insertion of an optically thick
permeable solid in the flame zone, where radiation
contributed so much to the energy transfer to the
load. Higher thermal efficiencies were obtained by
Kawamura et al. [12], who employed a design that
incorporates both internal and external heat recircu-
lations. The latter was accompli shed by a concentric
opposing heat exchanger to recover the exhaust gas
enthalpy. Sato et al. [13] obtained lean mixtures
with the flame sustaining flow rates as high as 40
times the burning velocity. A superior performance
was then realized in comparison to conventional
burners, wherein low NO
x
emission could be
obtained at the normal lean operation, but only
within a narrow range of combustible flow velocities.
Huang et al. [30] found that the initiation of
super-adiabatic wave combustion is dependent on
the amount of preheating energy. The smaller the
preheating firing rate, the more preheating energy
is required to sustain a stable flame. With the
increase in excess air, there was a rapid temperature
fall-off to the limit of extinguishment [11]. Such a
result necessitated the evaluation of gas and solid
temperatures’ sensitivities to different influencing
parameters, including the air–fuel ratio and the
flow velocity (as shown later ).
Babkin [31], Mital et al. [32], and Zhdanok et al.
[33] then clarified the dynamics of thermal and com-
bustion waves in porous media. They found that by
preheating a narrow porous zone and admitting the
gas mixture without combustion, there was a ther-
mal wave in a form of travelling temperature pe aks
with a constant velocity and decreasing amplitude.
By adjusting the filtration rate of the mixture so
that thermal and combustion waves overlap and
enhance each other, a stable combustion wave with
an associated localized super-adiabatic temperature
pulse was obtained. Their findings then defined a
speed of thermal wave propagation (as dependent
on the solid thermal conductivity, capacity, and
flow conditions) and a speed of combustion wave
propagation (which is related to the kinetic para-
meters that are coupled, in turn, to the thermal
wave propagation). For very lean mixtures, Kennedy
et al. [34] found the combustion wave velocity to be
close to that of the thermal wave. Their results moti-
vated a further work to speed up the combustion
wave velocity at the lean operation by a proper con-
trol of the relevant parameters.
3.2 Super-excess enthalpy recipro cating flow
system
A noticeable jump in obtaining super-adiabatic com-
bustion has occurred by the reciprocating flow
system, as investigated by Hanamura et al. [35, 36]
and Zhdanok et al. [37]. In such a system, the
combustibles flow in a certain direction, so that gas
and solid temperatures are established by the
mutual heat transfer process and both temperature
Combustion in porous media 489
JPE169
#
IMechE 2006 Proc. IMechE Vol. 220 Part A: J. Power and Energy
at University of Victoria on August 30, 2012pia.sagepub.comDownloaded from