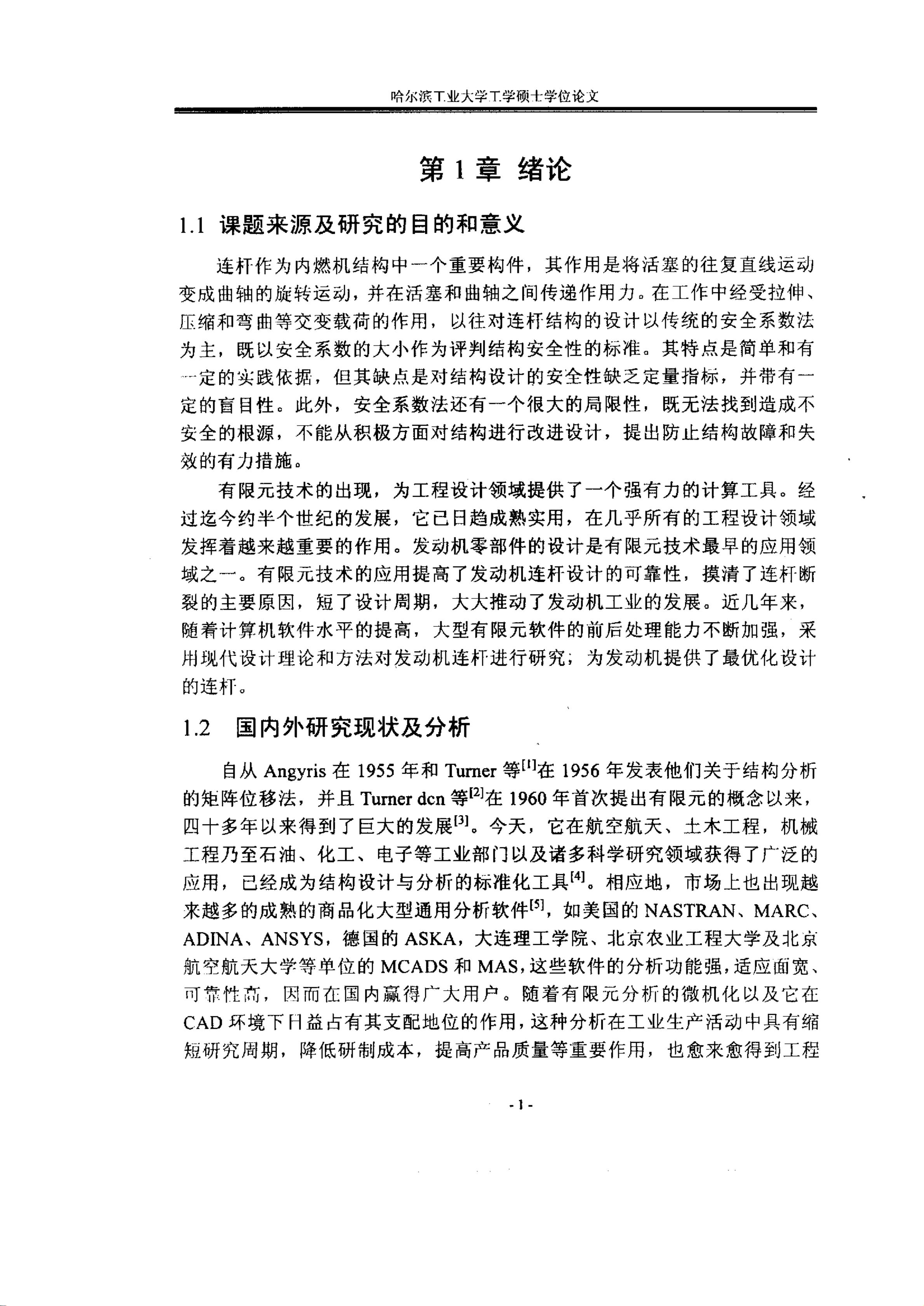

huihui8990
- 粉丝: 0
- 资源: 1
最新资源
- AI生成PPT(免费+收费)总汇
- CCD卷绕检测机sw18可编辑全套技术资料100%好用.zip
- 基于FPGA的自适应滤波器FIR IIR滤波器LMS NLMS RLS算法 FxLMS 分数阶 本设计是在FPGA开发板上实现一个自适应滤波器,只需要输入于扰信号和期望信号(混合信号)即可得到滤波输
- 单机版RS485集中抄表软件,集中抄读645-2007协议的智能电表,645-1997的没有测试过,不清楚能不能抄,本地485有线集中抄表,配合485转网络可实现远程抄表
- 数据分析-62-亿欧企业榜单探索
- AR贴膜主机(sw12可编辑+工程图)全套技术资料100%好用.zip
- 数据分析-63-基于逻辑回归模型的医疗数据分析(拟合度差)
- 半龙门伺服双点电阻焊机sw19全套技术资料100%好用.zip
- 板材定位送料机sw18全套技术资料100%好用.zip
- 黑猫消费者投诉数据集,数据量大概43000条
- 板料翻面滚筒输送机sw19可编辑全套技术资料100%好用.zip
- 2023胡润百富榜-品牌榜数据集
- 半自动螺钉拧紧机step全套技术资料100%好用.zip
- 永磁同步电机磁链、损耗计算模型,基于有限元仿真数据
- 玻璃清洗机器人sw18全套技术资料100%好用.zip
- labview编写的数据回放软件,支持多曲线回放,支持曲线缩放,支持曲线打标签,支持曲线勾选可见不可见,支持点击曲线加粗显示,支持点击曲线显示当前曲线Y标尺,支持曲线配置,支持红蓝标尺,支持曲线时间轴
资源上传下载、课程学习等过程中有任何疑问或建议,欢迎提出宝贵意见哦~我们会及时处理!
点击此处反馈


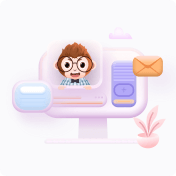