
huayuya123
- 粉丝: 27
- 资源: 31万+
最新资源
- go-zero和gorm构建的分布式微服务后端权限管理系统(含前端+后端完整 源码).zip
- GA优化BP神经网络项目-基于Python(含源码+项目说明+设计报告).zip
- Golang开发的微服务博客系统+设计文档资料等(包括博文、评论、用户服务等模块).zip
- Go语言编写的区块链可信对账系统(含源码及设计报告).zip
- Go语言构建的简易区块链demo实验(包含完整代码和指导手册).zip
- Go语言搭建多节点区块链网络实战指南(含源码及设计文档).zip
- Go语言开发微信视频号自动回复打招呼服务端项目源码+设计文档.zip
- GPT-SoVITS推理-中文情绪分析自动切换参考音含源码.zip
- Hyperledger Fabric支持的分布式身份可信认证区块链解决方案(含链码、启动脚本及SDK).zip
- IPCC2020初赛题目-Stencil代码实现+项目说明.zip
- Java开发基于SpringCloud-Kubernetes的微服务架构实例(含源码).zip
- JavaWeb前后端搜索服务系统-基于SpringBoot+Elasticsearch+SparkMLib开发(含源码+项目说明+实验报告).zip
- Jenkins+Kubernetes搭建自动化部署平台指南(附源码).zip
- JPEG图像压缩算法在STM32平台的实现(含源码+项目说明+主要算法介绍).zip
- k8s和Argo工作流结合构建的安全扫描器系统设计源码+设计文档.zip
- Kaggle猫狗分类竞赛-基于PyTorch(准确率超过99%,含源码+项目说明+设计报告).zip
资源上传下载、课程学习等过程中有任何疑问或建议,欢迎提出宝贵意见哦~我们会及时处理!
点击此处反馈


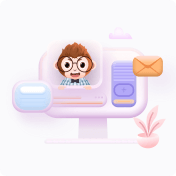