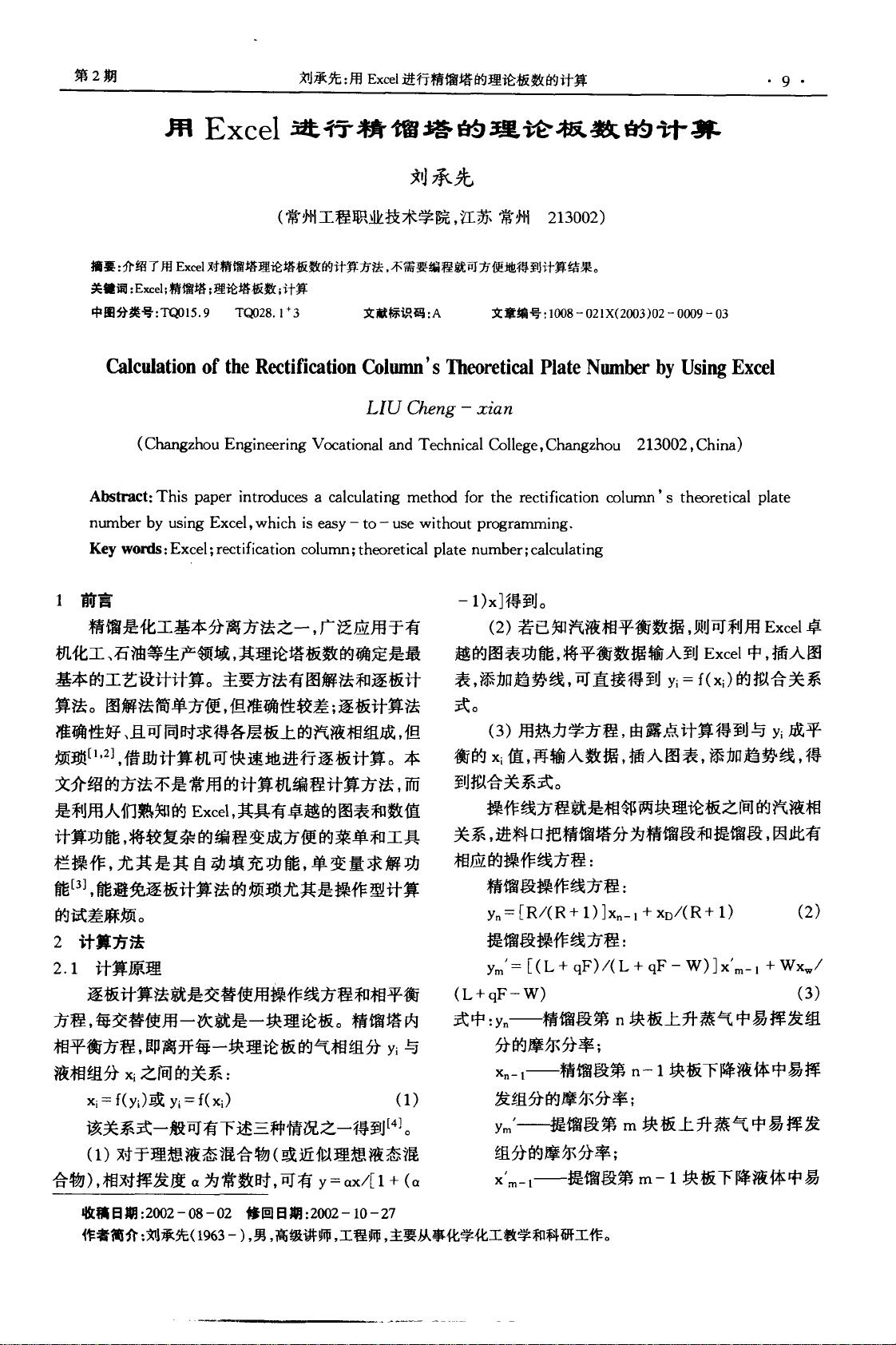
204
H. KLIMMEK
tallow fatty acids have been investigated on laboratory
scale. The results of the pretreatrnent/hydrogenation trials
are summarized in Table I. They ~ndicate that pretreatment
of the fatty acid with spent catalyst prior to hydrogenation
with fresh catalyst has some influence on catalyst consump-
tion. Approximately 40% Ni can be saved. The results
demonstrate that, at least in the case of tallow fatty acids,
TABLE I
Effect of Pretreatment of
Split Tallow Fatty Acid (IV
=
57.6)
on Hydrogenation
Rates ~
Run Pretreatment Final IV
47.3
1 a No pretrearment
1 b 9.6
41.3
2 a H a SO 4 wash
2b 4.5
3 a O. 1% Ni (fresh), with filtration 40.8
3b 4.2
4 a 0.1% Ni (spent), with filtration 37.8
4b 3.3
5 a 0.1% Ni (spent), no filtration 39.2
5b 4.4
6 a 0.05% Ni (spent), no filtration 41.3
6b 4.4
7 a Straight distillation 5.8
7b 1.0
t Standard hydrogenation conditions: 300 g fatty acid; 200 C;
bar; 850 rpm; 150 min.
Run a with 0.0625% Ni; run b with 0.25% Ni.
30
distillation is by far the most effective way to remove im-
purities adversely affecting the hydrogenation process.
Under the stated conditions a split tallow fatty acid yielded
an IV of 9.6, using 0.25% Ni. After a straight distillation of
the split tallow fatty acid, the corresponding hydrogenation
trial ended at an IV of 5.8, although only 0.0625% Ni was
applied.
There are also a few other methods of pretreating fatty
acids prior to hydrogenation, e.g., use of bleaching earth.
The cost of such purification steps has to be calculated and
compared with catalyst savings. The most economical way
will depend upon local circumstances.
ACKNOWLEDGMENT
G. Klauenberg provided technical assistance.
REFERENCES
1. Babuchowski, K., and A. Rutowski, Seifen, Oele, Fette,
Wachse 95:27 (1969).
2. Ottensen, I., Presentation at the 6th Scandinavian Symposium
of Fats and Oils, Grena, Denmark,
1971.
3. Mork, P.C., JAOCS 49:426 (1972).
4. Mork, P.C., and D. Norgard, JAOCS 53:506 (1976).
5. Drozdowski, B., and M. Zajac, JAOCS 54:595 (1977).
6. deMan, J.M., E. Pogorzelska and L. deMan, JAOCS 60:558
(1983).
7. Klostermann, K., and H. Hobert, J. Catal. 63:355 (1980).
8. Ottensen, I., and B. Jensen, Presentation at the ISF/AOCS
Congress, New York, 1980.
9. Coenen, J.W.E., and B.G. Linsen, Physical and Chemical As-
pects of Adsorbents and Catalysts, edited by B.G. Linsen,
Academic Press, London, 1970, p. 496.
10. Coenen, J.W.E., Fette, Seifen, Anstrichm. 77:341 (1975).
Fatty Acid Fractionation by Column Distillation:
Purity, Energy Consumption and Operating Conditions
HERMANN
STAGE, ATT-Verfahrenstechnik GmbH, Ludgeristrasse 9, 4400 MOnster,
West Germany
ABSTRACT
This paper discusses the optimal process conditions for production
of individual fatty acids of any desired purity up to higher than 99%
and describes especially the influences of column internals as well as
exchange numbers, reflux ratios and fatty acid residence times at
distillation temperatures. The new process conditions are character-
ized by degasification at low temperatures followed by efficient
dehydration together with separation of first cuts at high reflux
ratios by short-time dephlegrnation. The design of columns for effi-
ciency and low pressure drop is influenced by the thermal properties
of crude acids and the quality demands on distillate fractions, Envi-
ronmental requirements can be met by working without open
steam. Bottom temperatures should not exceed 250 C, to prevent
thermal degradation of fatty acids as well as corrosion of stainless
steel.
FATTY
ACID FRACTIONATION IN THE PAST
Industrial separation of individual fatty acids with high
purity by column distillation from raw acids of natural
origin such as from splitting different kinds of vegetable oils
or animal fats is a fairly new technique (1-7). This process
came into use mainly after World War II using bubble cap
or packed columns (8-13) with unsaturated open steam
(14) for lowering the evaporation temperatures to avoid
JAOCS, vol. 61, no. 2 (February 1984)
thermal degradation of the heat-sensitive fatty acids (15-
17). Early pioneers in this field were R. A. Potts and F. B.
White (1,8,9,11-14). More recently, the economics and
environmental regulations have changed decisively. Also the
demands for purity have increased greatly. Therefore, new
process principles became necessary which influenced
equipment construction as well as operation conditions
(18-26).
THE BASIS FOR A NEW FRACTIONATION PROCESS
The most important step in a new process was complete
removal of open steam as part of developing new high effec-
tive column construction with very low pressure drop,
together with new evaporation and condensation systems
(18-25). Besides using special distillation columns of low
pressure drop, today's process is characterized by effective
film degasification at moderately low temperatures, fol-
lowed by efficient dehydration together with separation of
the odor cut as first cuts at high reflux ratios by short-time
dephlegmation and a film-type pitch separation step. Ac-
cording to Figure 1, the precut step consists of a once-
through falling film evaporator as stripping section and an
enriching zone designed as dephlegmator column in the
评论0