非预期故障诊断通用模型和OCPCA实现
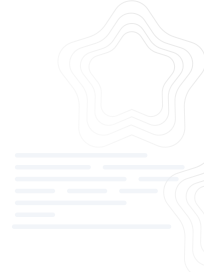


非预期故障诊断是工业自动化和智能系统中的一个重要领域,它涉及到设备或系统的异常检测与识别。通用模型的设计是为了能够适应各种复杂工况,提高故障识别的准确性和效率。本话题聚焦于“非预期故障诊断通用模型和OCPCA实现”,这是一种创新性的故障诊断策略,它利用了原创的OCPCA(One-Class Principal Component Analysis,单类主成分分析)方法。 OCPCA是一种无监督学习的模式识别技术,特别适用于异常检测。在传统的PCA(主成分分析)中,我们通常处理包含两类或多类数据的情况,而OCPCA则关注于正常模式的学习,通过分析正常状态的数据分布来构建模型,一旦出现偏离正常模式的行为,即被视为异常或故障。这种方法在处理非预期故障时尤其有效,因为它无需预先知道所有可能的故障类型,只需识别出与正常运行模式的偏离。 在TEP(Thermal Energy Plant,热能发电厂)这样的复杂系统中,非预期故障诊断至关重要。TEP由多个复杂的子系统组成,如燃烧、蒸汽生成、涡轮机和发电机等,任何一个环节的故障都可能导致整个系统的性能下降甚至停机。OCPCA模型应用于TEP,可以实时监控各个关键参数,及时发现潜在的问题,防止故障升级,保证电厂的安全稳定运行。 实现OCPCA模型通常包括以下几个步骤: 1. 数据预处理:收集TEP运行过程中的大量传感器数据,包括温度、压力、流量等,进行清洗和标准化,确保数据质量。 2. 主成分分析:对预处理后的数据进行PCA变换,降维并提取主要特征,这有助于减少数据的冗余,提高模型的计算效率。 3. 构建单类模型:基于正常运行状态的数据,训练OCPCA模型,学习正常模式的分布。 4. 异常检测:实时或定期将新的监测数据输入到模型中,通过比较新数据点与模型中的正常模式,判断是否存在异常。 5. 故障定位与识别:一旦检测到异常,结合系统知识和专家经验,定位故障发生的具体部位,并进一步识别故障类型。 这种方法的创新之处在于其灵活性和实用性。OCPCA模型不仅可以捕捉到广泛的故障模式,而且对于TEP这样动态变化的环境有很好的适应性。同时,由于它依赖于正常模式的建模,因此在数据有限或者难以获取故障样本的情况下,依然可以有效地进行故障诊断。 "非预期故障诊断通用模型和OCPCA实现"是一个将理论与实践紧密结合的领域,通过先进的数据分析技术解决实际工程问题,提高了故障诊断的智能化水平,对于保障工业系统的稳定运行具有重大意义。通过不断优化和改进模型,我们可以期待未来在更多领域看到这种技术的应用,以提升系统的可靠性与安全性。





































































































- 1
- 2
- 3
- 4

评论2
最新资源