
勾之月
- 粉丝: 695
- 资源: 6729
最新资源
- 基于PLC的乡村供水系统设计 有组态仿真,CAD电气原理图,IO分配表,组态仿真,程序,演示视频 (1)该恒压供水系统能够正常供水, 保证供水质量;该恒压供水系统具有手动操作方式和自动操作方式,两种
- 西门子1200博图编程电机控制程序块,1200和1500通用的 1.包括正转,反转,变频控制,模拟量,故障,故障复位,控制字来显示电机的6种状态等 2.底层使用SCl编程,直接可以导出库文件.
- 铌酸锂声光效应声表面波激发 氧化锌与Si体系 2D 3D 注:目前未进行声光耦合,只激发声表面波
- 永磁同步电机无感foc位置估算源码 PMSM FOCBLDC 带仿真模型和源代码 无刷直流电机无感foc源码,无感foc算法源码 1 速度估算位置估算的代码所使用变量全部用实际值单位,能非常直观的
- xilinx vivado verilog srio开发,包含维护包、读写和门铃等功能,顶层封装为fifo,操作简单,简单修改即可应用到实际工程中,附含srio使用说明文档和免费license
- 二自由度车辆动力学模型 软件使用:Matlab Simulink 适用场景:采用模块化建模方法,适用于多种工况场景 产品simulink源码包含如下模块: 包含模块: 二自由度车辆动力学模型 包含:
- 基于滞环电流控制的VIENNA整流器
- FX5U程序三菱plc程序案例模板,一个完整的项目 用三菱FX5U,一共控制4个轴,说明了定位控制中的公共参数设定、回原点、JOG手动、决对定位、相对定位、控制等部分,威纶程序报警界面.多个机种选择
- 直流电机双闭环调速系统,以及直流电机双闭环系统建模,采用转速外环电流内环的控制结构,稳态效果良好,动态响应也较好,需要可以直接联系,仿真模型加对应的报告
- 松下FP-XH系列PLC程序,昆仑通态触摸屏程序 松下+昆仑通泰多工位装配机项目,多工位转配机,实际案例,在多工位直线,转盘类应用,会了这个就懂了. 1.国际标准IEC规范化编程模板框架程序 2.伺服
- 基于FPGA的以太网TCP数据回环设计 vivado工程
- 39节点故障数据,不同短路点,不同短路持续时间,不同负荷水平,共计3000次仿真
- 基于51单片机的电子秤 #有计价功能: 1)HX711传感器称重 2)按键可调整单价 3)去皮、清除功能 4)超重报警 5)可保存到小数点后三位 文档包含: 仿真、程序、原理图、PCB、报告
- T型三电平逆变器仿真模型,闭环控制,三电平SVPWM算法,可提供参考文献
- 光伏电池仿真模型,PV
- 二极管钳位,五电平SPWM仿真模型
资源上传下载、课程学习等过程中有任何疑问或建议,欢迎提出宝贵意见哦~我们会及时处理!
点击此处反馈


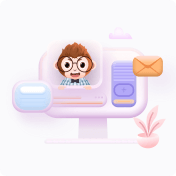
评论0