
dchw66
- 粉丝: 26
- 资源: 18万+
最新资源
- MATLAB代码,LSTM(长短时记忆模型),粒子群优化LSTM(psolstm),量子粒子群优化LSTM(QPSOLSTM),可用于风电、光伏等负荷预测,时序预测,数据为单输入单输出,更数据简单,导
- 蒙特卡洛模拟电动汽车充电负荷特性 主要内容: 利用蒙特卡罗仿真生成大规模电动汽车无序充电功率曲线,分析大规模电动汽车接入对电网造成的影响 包括电动汽车日行驶里程概率分布,起始充电时间概率分布,耗电
- PMSM BLDC参数辨识工程源码,电阻电感和完全解耦FOC算法模块 无刷直流电机参数辨识代码 电阻电感磁链参数 含已经解耦的FOC算法模块 辨识精度和收敛速度好 很方便移植到你自己的工程里面 内含使
- 一个定时器控制8路舵机,一个定时器控制8路舵机,含舵机的其他速度控制代码 软件和教程资料
- FX5U Active Socket TCP通讯FB 功能块 有几个通道,就拖几个FB,FB里面全部用的相对地址,相互之间不受干扰 通道0~7 共8个 使用的是上电直接SM402自动连接,
- 四旋翼飞行器自适应或Pid姿态位置控制,可以对比输出,也可以选择其中一种算法输出,包含多个性能指标输出,可直接运行
- 储能PCS逆变器双向变流器设计方案资料,双向DCDC和三电平逆变PCS 30KW 成熟已量产 1.此系列为30KW储能PCS逆变器设计方案资料,双向DCDC和三电平逆变PCS; 2.仿真源码含有并网
- 模块化多电平变器MMC两种调制策略实现(交流3000V-直流5000V整流)仿真,单桥臂二十子模块,分别采用最近电平逼近NLM与载波移相调制CPS-PWM实现,仿真中使用环流抑制,NLM中采用快速排序
- MATLAB SIMULINK,MMC整流器仿真,双闭环控制,最近电平逼近调制,冒泡排序法,在2.5秒加入环流抑制,n=18,仅供学习参考,欢迎讨论,共同进步
- 光伏单相并网仿真 前级采用boost升压电路,采用变扰动观察法实现最大功率点追踪,追踪效果良好 后级采用双闭环控制,电压外环,pr电流内环,陷波器踢出二次功率脉动 单相锁相环采用基于广义二阶积分矢
- 汽车ABS防抱死系统,基于Carsim和Simulink的联合仿真模型 四轮均具有ABS系统,控制目标为四个制动缸压力 采用的是逻辑门限值方法 通过MATLAB状态机对abs系统增压,减压,保压
- 永磁同步直线电机 高阶非奇异快速终端滑模控制 控制效果如下图,提供参考文献和公式 注:控制参数非最优,仅供需要的同学参考
- RRT路径规划算法代码(MATLAB版本) 基于rrt算法的路径规划算法matlab代码,求解常见的路径规划问题 内含算法的注释,模块化编程,新手小白可快速入门 rrt算法,路径规划算法
- 研究背景:高斯光束整形为贝塞尔光束后,可以实现激光功率密度的进一步集中,从2mm的高斯光斑转变为10um左右的贝塞尔光斑,贝塞尔光束因高功率密度的特性,可以用于切割,由于超快激光特性,热影响区小,切割
- 级联H桥型statcom的Matlab仿真,可实现对三相电网的无功补偿(感性和容性),以及直流测电容电压平衡控制 所针对的电网系统为10kV,50Hz,主电路为级联h桥逆变器(CHB),在仿真中CH
- 编码器foc工程源码 编码器为1000线ABZ编码器 源码中含有foc初始电角度差的获取方法 模块化编程 非常适合工业量产和移植
资源上传下载、课程学习等过程中有任何疑问或建议,欢迎提出宝贵意见哦~我们会及时处理!
点击此处反馈


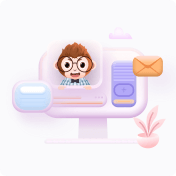