
dchw66
- 粉丝: 27
- 资源: 18万+
最新资源
- 线控转向系统:基于Carsim与Simulink联合仿真的控制策略与模型研究,线控转向系统:基于Carsim与Simulink联合仿真的控制策略与模型研究,线控转向系统联合仿真模型及控制策略研究 描述
- 基于python的订单管理系统
- 基于新算法SSA优化的变分模态分解风电功率分配策略:混合储能高效利用,创新性显著,基于新算法SSA优化的变分模态分解风电功率分配策略:混合储能高效利用与参数优化策略,基于新算法SSA优化变分模态分解的
- 【bussiness-DC】
- 使用BE、FE及C N方法求解一维扩散方程的Matlab实现,使用BE(向后欧拉)与FE(向前欧拉)算法及C N方法在Matlab中求解一维扩散方程的数值分析研究,使用BE(向后欧拉),FE(向前欧拉
- 博图16 PLC控制的4x5立体车库系统:包含运行效果视频、接线图及IO表全解析,4x5立体车库控制系统详解:博图16 PLC运行效果视频、接线图及IO表一览,4x5立体车库控制系统 博图16 带PL
- Python 智能机房签到系统:高效管理课堂考勤
- 进程上下文详细分析PDF原文
- 基于拉丁超立方采样与自适应核密度估计的电力系统概率潮流精准计算,基于拉丁超立方采样的电力系统概率潮流计算:自适应核密度估计与带宽优化的方法研究,采用拉丁超立方采样的电力系统概率潮流计算 (自适应核密度
- numpy-2.2.0-cp310-cp310-win32.whl
- numpy-2.2.0-cp310-cp310-win_amd64.whl
- 仅作测试无意义1111111111111111
- 基于PWM的 三色灯RGB模块调色 HAL库
- 商业数据分析BI+人工智能AI.zip
- 伺服驱动系统中的FPGA实现:电流环、速度环与位置环的协调控制,包含坐标变换及电机反馈接口,SVPWM技术,以及在FPGA中实现的编码器协议,伺服驱动FPGA电流环:实现坐标变换、电机反馈与SVPWM
- 基于PWM的 三色灯RGB模块调色 寄存器 代码
资源上传下载、课程学习等过程中有任何疑问或建议,欢迎提出宝贵意见哦~我们会及时处理!
点击此处反馈


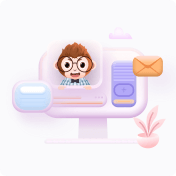