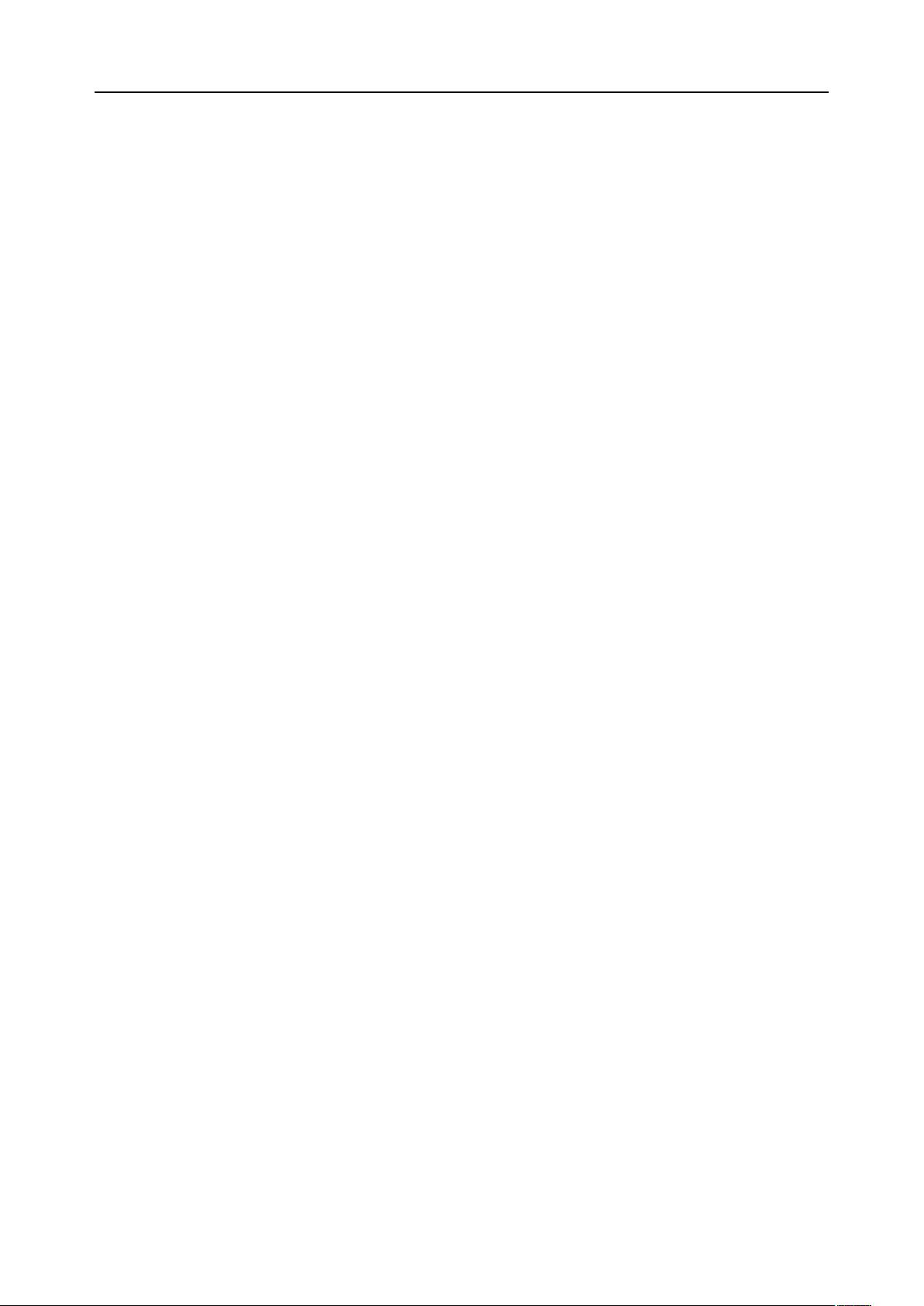
influence of external interference on the controlled parameters as much as possible, so as to make
the production process stable. So the choice of control strategy and control algorithm is very
important.
3. Design process of liquid level control system of double tank
Determine the control objective: the control objective of the double tank is to meet the
control requirements of the tank level within the allowable error range. Select the controlled
parameters: the controlled parameters are the controlled quantity or system output, in this paper,
the liquid level of the water tank. No matter what control scheme is adopted, it is necessary to
control or monitor the production process through the detection of some parameters. When some
parameters are not easy to be measured directly, it can be calculated by indirect parameters which
have a function relationship with the direct controlled quantity. In this paper, the liquid level of
the water tank can be measured directly, so the controlled parameter is the page height of the
water tank. Selection of control quantity: the control quantity is determined by the production
process. In a controlled process, there are multiple controlled quantities. Which control quantity
to use depends on the control requirements. In this paper, the control quantity is very clear, that is,
the opening of the valve. Determine the control scheme: the control scheme is one of the core
contents of the whole design. With the different control objectives and control accuracy
requirements, the control scheme also changes. Selection of control strategy: the controlled
process determines the controlled strategy. For a simple controlled process, the conventional PID
control strategy can meet the control requirements. With the complexity of the controlled process,
it is necessary to consider the use of complex control strategies such as fuzzy control, decoupling
control and so on. In this paper, the PID control strategy is used to control the double tank.
Commissioning, debugging and parameter setting of the regulator of the system: before all the
designs are completed, the parameters must be continuously debugged to make the system
performance reach the optimal state.
The selection of controlled process can directly reflect the output and quality of products in
the production process, and is easy to parameter. In the double tank control system, the liquid
level of the lower tank is selected as the controlled parameter of the system, because the lower
level is the key of the whole control function, and it is required to maintain the liquid level above
and below a given value. If its regulation will cause the failure of the whole system control design,
and now there are mature technologies for liquid level measurement, including direct reading
liquid level meter, buoyancy liquid level meter, static pressure liquid level meter, electromagnetic
liquid level meter, over liquid level meter, etc.
4. PID algorithm and research of double tank liquid level control system
In industrial production, liquid level is an important controlled quantity of process control
system, especially in petroleum, chemical industry, environmental protection, water treatment,
metallurgy and other industries. In the automation of industrial production process, it is often
necessary to measure and control the liquid level of some equipment and containers. Through the
detection and control of liquid level, we can know the quantity of raw materials, semi-finished
products or finished products in the container, so as to adjust the balance of input and output
materials in the container, and ensure the proper matching of materials in each link of the
production process. The control computer can continuously monitor the operation process of
production, monitor or control the liquid level of the container in time, and ensure the quality and