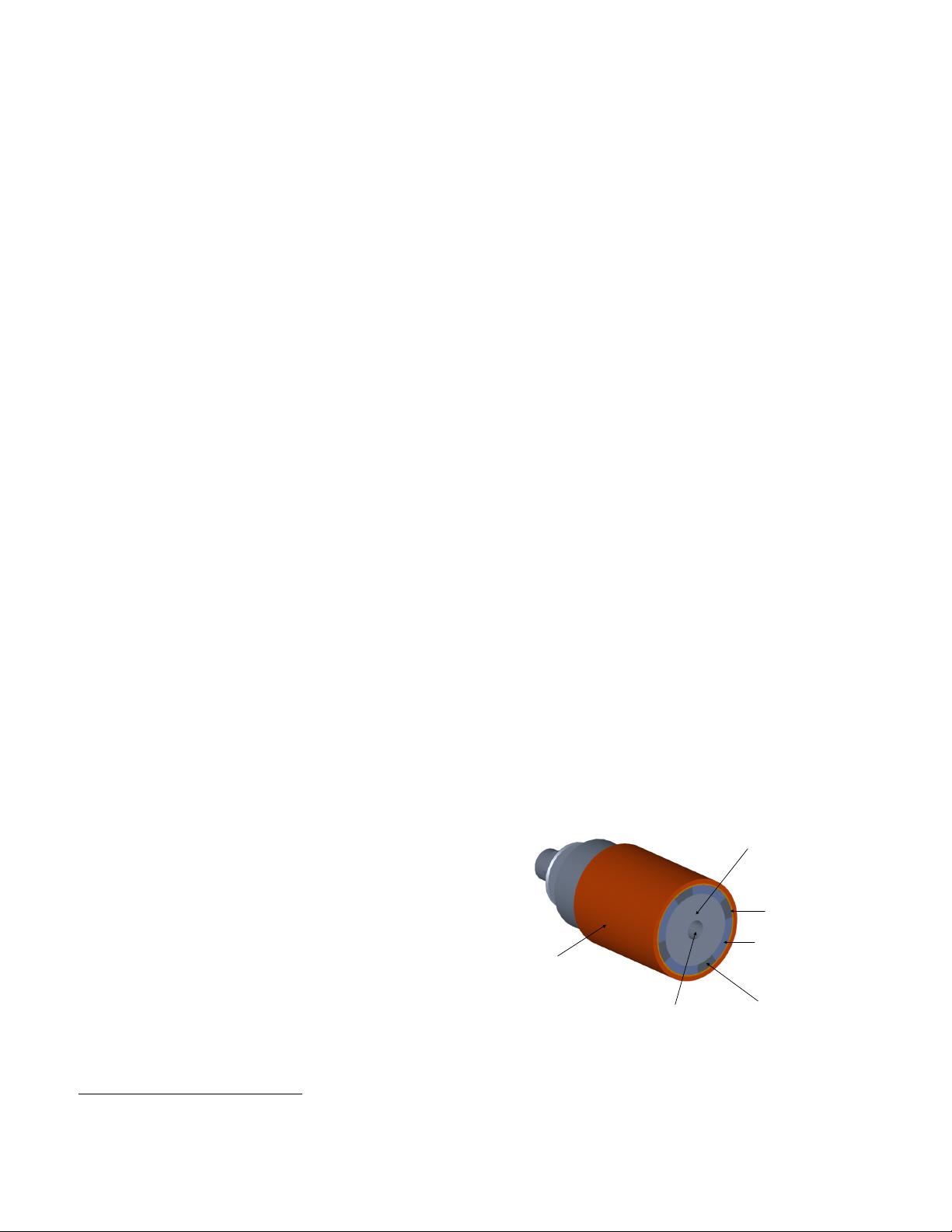
Thermal analysis of a high-speed generator
O. Aglén
Dept. of Electrical Engineering
KTH The Royal Institute of Technology
SE 100 44, Stockholm, Sweden
Å. Andersson
ABB Automation Technologies
Motors & Machines / LV Motors
SE 721 70, Västerås, Sweden
Abstract
1
- The machine under study is a permanent magnet
synchronous generator intended for operation at high speeds
together with a micro-turbine in a Combined Heat and Power
(CHP) unit. Target power is 110 kW at 70 000 rpm. The study is
both theoretical and experimental since it includes calculation of
loss distribution and thermal analysis together with calorimetric
measurements of losses and temperature measurements. In this
paper the thermal model is described. Using results from loss
calculation and calorimetric measurements a thermal analysis is
carried out. It is shown that introducing a copper screen in the
rotor reduces the losses to acceptable values. A limit for the
allowable rotor losses is given.
I. INTRODUCTION
In areas where the grid has reached its power limit, in
remote areas or in countries with low transmission
capabilities, installing small power units, where they are
needed, can be more cost efficient than building large power
plants and power lines, at least it is much quicker. A compact
microturbine Combined Heat and Power (CHP) unit can offer
low emissions, fuel flexibility and high efficiency. The
system is described further in [1]. It uses a high-speed
generator operating in the speed range 50 000 rpm to 70 000
rpm. A thermal analysis based on results from calculations
and measurements of one generator prototype is carried out.
The thermal model is described in this paper.
II. T
HE GENERATOR
The electric power is generated in a high-speed permanent
magnet synchronous generator, which is integrated with the
microturbine. The rotor is suspended by one bearing on each
side of the permanent magnet rotor and there are no
additional bearings on the turbine shaft. The stator core is
made with thin laminations of low-loss electrical steel and the
winding is made with Litz-wire to achieve good high-
frequency characteristics. The four-pole design contributes to
short end-windings that make possible a short distance
between bearings. Although the efficiency is high, water-
cooling is used to keep the temperature low in the winding as
well as in the magnets. Together with vacuum pressure
impregnation and thicker than standard insulation this ensures
a long lifetime of the winding.
The rotor consists of a magnetic steel body with surface
mounted permanent magnets as shown in Fig. 1. A carbon-
fiber bandage retains the magnets even at 70000 rpm.
TABLE I GENERATOR DATA
Stator core outer diameter 135 mm
Stator core length 160 mm
Rotor outer diameter 66 mm
Rated voltage 500 V
Rated speed 70 000 rpm
Rated power 110 kW
An important issue is to ensure that the rotor never reaches
the temperature that would de-magnetize the magnets or
drastically reduce the lifetime of the carbon-fiber bandage.
This is done both by reducing the rotor losses and by
providing efficient cooling in the air-gap. Two main factors,
air friction and asynchronous mmf-waves in the air-gap cause
a temperature rise in the rotor. The latter are mainly caused
by stator current time harmonics. Since the carbon-fiber
bandage acts like a thermal insulator, the rotor is more
sensitive to current harmonics than a rotor in a conventional
machine.
Conceptual methods of rotor loss reduction are filters,
special modulation patterns in the power electronics and
multilevel converters. These methods reduce the effect of
harmonics in the stator current. In principal the problem can
be solved with a filter only. If the output current is perfectly
sinusoidal the rotor losses due to time harmonics are zero.
Although possible it is not always the most cost efficient
method.
The machine under study was made to operate together
with a, more or less, standard three-phase converter without a
filter for current harmonics.
Magnetic shaft
Screen
(optional)
NdFeB magnet
Pole separator
(could be part of
magnet or shaft)
Center hole
(optional)
Retaining cylinder of
composite bandage
Magnetic shaft
Screen
(optional)
NdFeB magnet
Pole separator
(could be part of
magnet or shaft)
Center hole
(optional)
Magnetic shaft
Screen
(optional)
NdFeB magnet
Pole separator
(could be part of
magnet or shaft)
Center hole
(optional)
Retaining cylinder of
composite bandage
Fig. 1. Cut-away view of the generator rotor
0-7803-7883-0/03/$17.00 © 2003 IEEE
547