
beibeidzh
- 粉丝: 8
- 资源: 24万+
最新资源
- RyTuneX(系统优化工具)v0.9.1优化系统资源.mp4
- RyTuneX(系统优化工具)v0.9.0优化系统资源.mp4
- screenwings 反录屏截屏工具.mp4
- Epic免费喜+1《土豆兄弟》.mp4
- Epic免费喜+1《指环王:重返摩瑞亚》.mp4
- Flash Player(Flash插件) v34.0.0.323 官方版.mp4
- Funko Fusion一场动作冒险游戏动作冒险.mp4
- Gopeed一款多线程下载器 v1.6.3.mp4
- H5自适应响应式相册图片网站模板 – 图片壁纸类网站源码下载.mp4
- html5带音乐背景的圣诞节倒计时页面代码.mp4
- InternetTest Pro(网络测试工具)v8.7.0.2411.mp4
- LOL英雄联盟2012怀旧网单.mp4
- MacroDroid(任务自动化) v5.49.110 高级版.mp4
- MacOS录屏软件-QuickRecorder 1.5.4 【开源软件】.mp4
- M3U8多线程下载器支持断点续传边下边播.mp4
- Noad影视app 涵盖电影电视剧等.mp4
资源上传下载、课程学习等过程中有任何疑问或建议,欢迎提出宝贵意见哦~我们会及时处理!
点击此处反馈


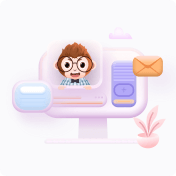